Unlocking the Potential of CFD for Lubrication Solutions
Optimizing Lubrication Systems with Computational Fluid Dynamics (CFD) In today’s advanced engineering landscape, Computational Fluid Dynamics (CFD) for lubrication is a game-changer. This powerful tool enhances our understanding of fluid mechanics and its impact on lubrication systems, providing an unparalleled approach to optimizing performance and efficiency in various mechanical applications. By utilizing advanced CFD simulation […]
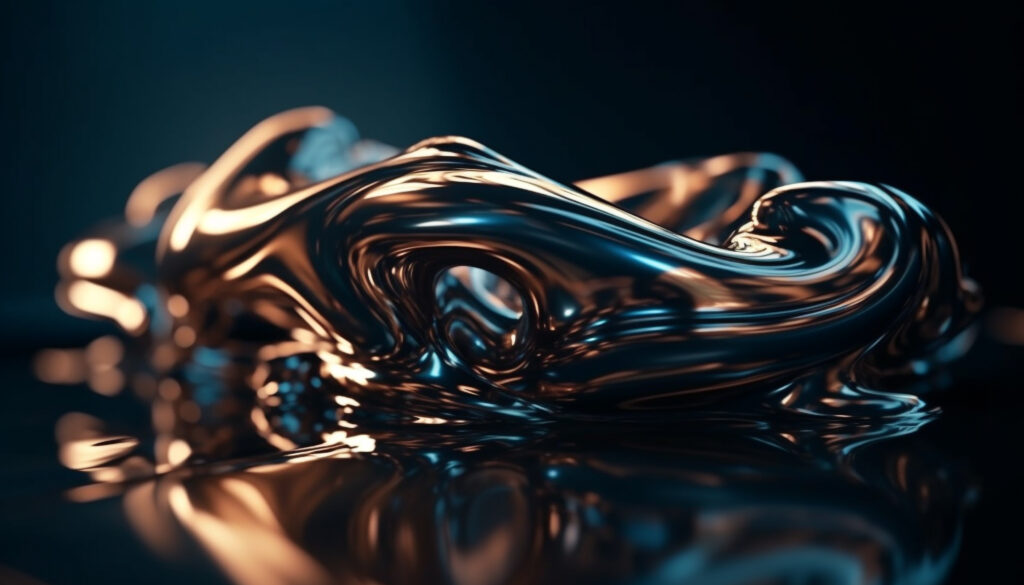
Optimizing Lubrication Systems with Computational Fluid Dynamics (CFD)
In today’s advanced engineering landscape, Computational Fluid Dynamics (CFD) for lubrication is a game-changer. This powerful tool enhances our understanding of fluid mechanics and its impact on lubrication systems, providing an unparalleled approach to optimizing performance and efficiency in various mechanical applications.
By utilizing advanced CFD simulation techniques, engineers and researchers can achieve precise control over lubrication processes, significantly improving the durability and efficiency of mechanical components.
Understanding CFD and Lubrication Systems
Computational Fluid Dynamics (CFD) is a branch of fluid mechanics that uses numerical analysis and algorithms to solve and analyze problems involving fluid flows. By simulating the behavior of fluids, CFD provides deep insights into the complex interactions between lubricants and mechanical systems.
This technology is particularly beneficial for lubrication systems, where understanding the fluid dynamics is crucial for optimizing performance and reducing wear.
CFD Modeling for Lubrication Systems
At the core of CFD modeling for lubrication systems is the ability to simulate the behavior of lubricants under various operating conditions. CFD tools allow engineers to visualize how lubricants move through systems, interact with surfaces, and respond to changes in pressure and temperature.
This capability is essential for designing lubrication systems that are both efficient and reliable. For instance, CFD can simulate the flow of lubricants in bearings, gears, and other critical components, helping to identify potential issues such as cavitation, which can lead to premature failure.
By understanding these dynamics, engineers can make informed decisions about lubricant selection, system design, and operating conditions to ensure optimal performance.
Optimizing Lubricant Flow
Optimizing lubricant flow is another critical application of CFD in lubrication systems. Proper lubricant distribution is vital for minimizing friction and wear, ensuring that all moving parts are adequately lubricated without excess that can lead to energy losses or overheating.
Using CFD, engineers can design lubrication systems that distribute lubricants evenly and efficiently throughout the machinery. This involves optimizing the pathways and channels through which the lubricant flows, adjusting flow rates, and ensuring that the lubricant reaches all critical areas. By doing so, the overall performance and longevity of the machinery are significantly enhanced.
Reducing Friction and Wear
One of the most significant benefits of CFD analysis in lubrication is its ability to reduce friction and wear in mechanical components. Friction is a major cause of wear and tear, leading to decreased efficiency and increased maintenance costs. By leveraging CFD, engineers can analyze how lubricants interact with surfaces and identify ways to minimize friction.
CFD simulations can reveal areas where friction is highest and suggest modifications to the lubrication system or the lubricant itself to reduce this friction. This might involve changing the viscosity of the lubricant, adjusting flow rates, or redesigning components to create smoother interactions. The result is enhanced durability and reliability of mechanical systems, translating to longer service life and reduced maintenance needs.
Thermal Management in Lubrication
Thermal management is another critical aspect where CFD proves invaluable. Lubricants not only reduce friction but also play a crucial role in dissipating heat generated by mechanical operations. Overheating can lead to lubricant degradation, increased wear, and even catastrophic failure of components.
By using CFD to analyze the thermal properties of lubricants, engineers can ensure that the lubrication system effectively manages heat. This involves understanding how heat is generated and transferred within the system, and how the lubricant contributes to cooling. CFD simulations can help in designing systems that maintain optimal temperatures, preventing overheating and maintaining system efficiency.
Innovative Lubrication Techniques
As technology advances, so do innovative lubrication techniques. CFD is at the forefront of these advancements, enabling the development of cutting-edge solutions for lubrication challenges. For example, nano-lubricants, which incorporate nano particles to improve lubrication properties, can be analyzed and optimized using CFD.
Additionally, CFD allows for the exploration of new lubrication methods such as hydrodynamic and elasto hydro dynamic lubrication, which involve complex interactions between lubricants and surfaces. These methods can be fine-tuned through CFD simulations to achieve the best possible performance in various applications.
Incorporating CFD for Lubrication: A Strategic Advantage
By incorporating CFD for lubrication, engineers and researchers can achieve significant improvements in machine efficiency and lifespan. The precise control over lubrication processes afforded by CFD leads to more effective and reliable systems. This is particularly important in industries where equipment downtime and maintenance costs can have substantial economic impacts.
Staying Informed About the Latest Advancements
The field of CFD and lubrication is continually evolving, with new advancements and techniques emerging regularly. Staying informed about these developments is crucial for engineers and researchers who aim to keep their systems running smoothly and efficiently.
Engaging with the latest research, attending conferences, and participating in professional networks are all ways to stay up-to-date with the latest in CFD simulations for lubrication.
Unlock the Future of Lubrication Technology with CFD
Computational Fluid Dynamics (CFD) is a powerful tool that offers significant benefits for lubrication systems. From CFD modeling for lubrication systems to optimizing lubricant flow, reducing friction and wear, and thermal management, CFD provides comprehensive solutions that enhance the performance and longevity of mechanical components.
By staying ahead with innovative lubrication techniques and incorporating the latest CFD simulations for lubrication, engineers can ensure their systems operate efficiently and reliably. Unlock the future of lubrication technology with CFD and explore our comprehensive resources and expert guidance on utilizing CFD for optimal lubrication solutions.