The Undercut in Gear Design: Importance and Applications
The Undercut in Gear Design: Its Importance and Applications What is the Undercut in Gear Design? In gear design, precision is paramount, especially when working with hardened gears for complex machinery. One concept that plays a crucial role in ensuring smooth operation and longevity of gears is the undercut. This design feature, while often overlooked, […]

The Undercut in Gear Design: Its Importance and Applications
What is the Undercut in Gear Design?
In gear design, precision is paramount, especially when working with hardened gears for complex machinery. One concept that plays a crucial role in ensuring smooth operation and longevity of gears is the undercut. This design feature, while often overlooked, holds significant importance in the proper functioning of industrial robots, automotive drive trains, and other complex mechanical systems.
Undercut refers to the intentional removal of material from the base of a gear tooth. This process helps in preventing interference when gears mesh. While the concept might seem straightforward, it is an essential aspect of gear design that can affect the durability and functionality of hardened gears. In this article, we will discuss the importance of undercut in gear design, its applications, and how it contributes to overall gear efficiency.
The Role of Undercut in Gear Design
Gears are complex mechanical components that transmit motion and force in machines. The design of gear teeth is highly specialized, as even the smallest deviations can lead to performance issues. The undercut, which involves removing material from the base of a gear tooth, ensures that gears mesh properly, preventing interference between the teeth.
When gears rotate, the undercut allows the teeth to engage smoothly without binding or causing excessive wear. This is particularly important in gears made from hardened materials, where improper meshing can cause catastrophic failure or shorten the lifespan of the gear. In hardened gears, the undercut is designed to accommodate the additional stresses that occur due to the increased hardness and brittleness of the gear material.
How the Undercut Prevents Interference in Gears
Interference is a major issue in gear systems, especially in hardened gears where the material is less forgiving. When gear teeth are designed without an appropriate undercut, the teeth may collide or scrape against each other during rotation. This can cause wear and tear, increase friction, and ultimately lead to gear failure.
By incorporating an undercut into the gear design, engineers ensure that the teeth engage smoothly. The removal of material from the base of the tooth reduces the chance of interference, allowing for better load distribution and more efficient power transmission. This is especially important in high-stress applications like automotive drivetrains and industrial robots, where performance and reliability are critical.
Applications of Undercut in Complex Machinery
The undercut in gear design finds application in various industries where precision and durability are required. Two of the most prominent applications are in industrial robotics and automotive drivetrains. In these industries, gears are subjected to extreme loads and must operate flawlessly under harsh conditions.
Industrial Robots
In the world of industrial robotics, precision and smooth operation are key to the success of any automated system. Robots rely on intricate gear systems to perform complex tasks with accuracy and efficiency. The use of undercut in gear design ensures that the gears within these robots can handle high-speed, high-torque operations without binding or causing excessive wear.
Hardened gears used in robotics often undergo intense loads during operation, making the inclusion of an undercut even more important. The undercut allows the gears to mesh properly and distribute the load evenly, ensuring that the robot operates smoothly and efficiently. This is especially important in applications where robots perform repetitive tasks over long periods, as the gears must be able to withstand prolonged use without failure.
Automotive Drivetrains
In automotive drivetrains, gears play a crucial role in transmitting power from the engine to the wheels. These gears must be designed to handle extreme forces and ensure smooth power delivery to maximize vehicle performance. The undercut in gear design is particularly important in hardened gears, which are commonly used in drivetrains due to their strength and durability.
Without an undercut, the meshing of gears in a drivetrain could result in interference, leading to excessive wear or even gear failure. The undercut allows for proper gear engagement, reducing friction and improving the efficiency of power transmission. This not only enhances vehicle performance but also increases the lifespan of the drivetrain components, making the undercut an essential aspect of gear design in the automotive industry.
Why the Undercut is Crucial for Hardened Gears
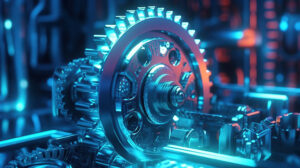
Hardened gears are used in high-stress applications due to their superior strength and resistance to wear. However, the increased hardness of these gears also makes them more brittle, which can lead to problems if the gears are not designed correctly. The undercut plays a critical role in preventing failure in hardened gears by ensuring smooth engagement and reducing the risk of tooth breakage.
When designing hardened gears, engineers must carefully calculate the depth and shape of the undercut to ensure that it provides adequate clearance without compromising the strength of the gear tooth. This balance is crucial for maintaining the performance and longevity of hardened gears in demanding applications such as industrial robots and automotive drivetrains.
How Undercut Affects Gear Strength and Durability
While the undercut is essential for preventing interference, it also has an impact on the overall strength of the gear tooth. Removing material from the base of the tooth can reduce its load-carrying capacity, especially in hardened gears where the material is more brittle. To mitigate this effect, engineers use advanced design techniques to ensure that the undercut provides the necessary clearance while maintaining the integrity of the gear tooth.
In hardened gears, the undercut must be carefully controlled to avoid weakening the gear while still providing the benefits of reduced interference and smoother meshing. By optimizing the design of the undercut, engineers can create gears that are both strong and durable, even in high-stress environments.
Designing the Perfect Undercut for Gear Systems
Designing the perfect undercut for gear systems requires a deep understanding of gear geometry and material properties. Engineers must consider factors such as the gear’s material, the load it will be subjected to, and the operating conditions of the machinery. For hardened gears, the undercut must be precisely calculated to ensure that it provides the necessary clearance without compromising the strength of the gear tooth.
The depth and angle of the undercut are critical design parameters that affect the performance of the gear system. If the undercut is too deep, it can weaken the gear tooth, making it more prone to breakage. If it is too shallow, the gears may not mesh properly, leading to interference and excessive wear.
Using Advanced Software for Gear Design
Modern gear design often involves the use of advanced computer-aided design (CAD) software to optimize the undercut and other features of the gear tooth. These tools allow engineers to simulate the performance of the gear system under various conditions, ensuring that the undercut is designed to provide the best possible performance.
By using CAD software, engineers can create highly optimized gear designs that are both efficient and durable. This is especially important for hardened gears, where precision is critical to ensuring the longevity of the gear system.
The Undercut’s Vital Role in Gear Design
The undercut in gear design is a small but crucial feature that plays a vital role in ensuring the smooth operation and longevity of gear systems. Whether used in industrial robots, automotive drivetrains, or other complex machinery, the undercut helps prevent interference, reduce wear, and improve the efficiency of power transmission.
For hardened gears, the undercut is especially important, as it allows the gears to withstand the additional stresses associated with high-load applications. By incorporating the undercut into gear design, engineers can create more reliable, durable, and efficient gear systems.
As we continue to push the boundaries of technology and engineering, the importance of precise gear design will only grow. The undercut, though small, will remain an essential feature in the design of high-performance gears, ensuring that machines run smoothly and efficiently for years to come.