The Role of Gear Technology in Robotic Industries
Optimizing Efficiency and Precision in Robotic Joints In the world of robotics, precise and controlled motion is essential. At the core of this precision lies gear technology, which plays a crucial role in determining the efficiency and functionality of robotic systems. Gears are fundamental in robotic joints, allowing for smooth and accurate movement. Without them, […]
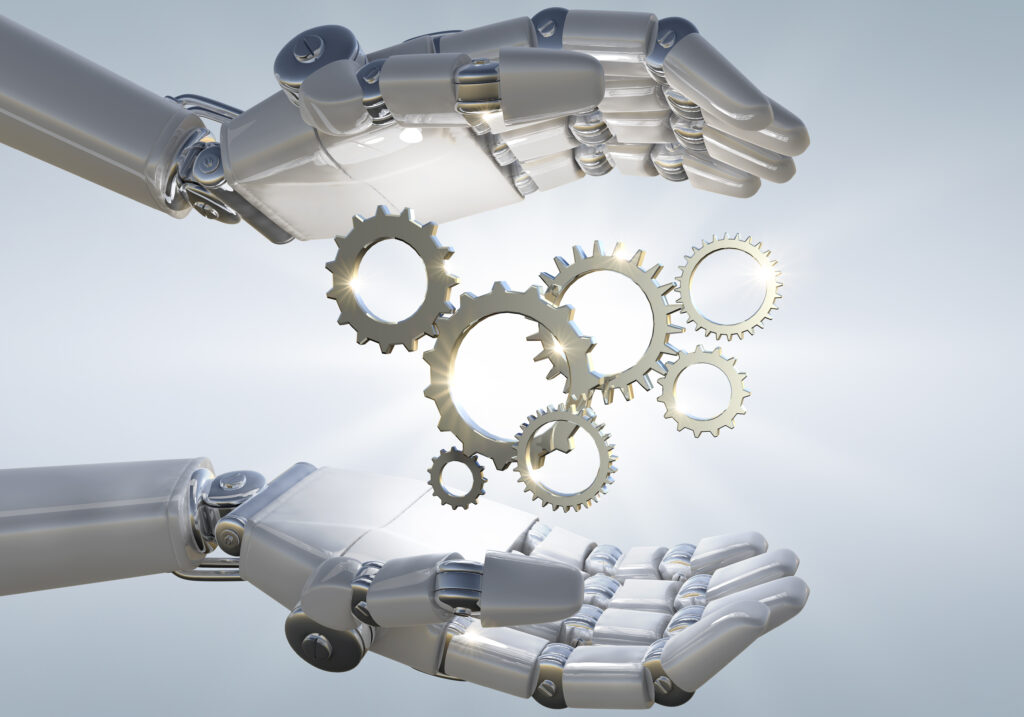
Optimizing Efficiency and Precision in Robotic Joints
In the world of robotics, precise and controlled motion is essential. At the core of this precision lies gear technology, which plays a crucial role in determining the efficiency and functionality of robotic systems. Gears are fundamental in robotic joints, allowing for smooth and accurate movement. Without them, robots would struggle to achieve the level of control and flexibility needed for tasks ranging from industrial automation to surgical procedures.
The Importance of Gears in Robotic Joints
Robotic joints are a key component of any robotic system. These joints, much like human joints, allow the robot to move and perform tasks in a variety of ways. Gears are what enable these joints to function with precision. By transmitting torque and adjusting rotational speeds, gears help achieve controlled movements necessary for complex robotic actions.
Image Courtesy: Freepik
How Gears Work in Robotics
Gears in robotics typically work by transferring power from motors to different parts of the robotic system. The gears modify the torque, speed, and direction of motor-driven movement. This allows robots to execute tasks with a high degree of precision.
Example of Gear Types in Robotic Joints
- Spur gears: Commonly used for straightforward, low-speed applications.
- Helical gears: Preferred for high-speed operations due to their smoother engagement and reduced noise.
- Planetary gears: Essential in applications requiring high torque and precision.
Each of these gears plays a specific role, ensuring that the robot’s joints move smoothly and efficiently. By altering the torque and speed, gears allow robotic joints to adapt to various demands, such as lifting heavy objects or performing delicate, high-precision tasks.
Enhancing Robotic Efficiency with Gear Technology
Gears directly impact the efficiency of robotic joints. The efficiency of a gear system depends on the gear type, material, and how well the gears are meshed. Properly designed gears ensure minimal energy loss during transmission, which means that robots can perform tasks faster and with less energy consumption. This is particularly important in applications such as manufacturing, where robots need to operate continuously without overheating or breaking down.
Moreover, gears reduce the wear and tear on motors by distributing loads more effectively. This extends the lifespan of robotic systems, minimizing maintenance costs and downtime.
Precision in Robotic Movements
Precision is one of the most critical requirements in robotics. Whether it’s assembling intricate parts in manufacturing or performing delicate surgeries, robots need to move with a high level of accuracy. Gear technology is what makes this possible. By offering smooth and controlled transmission of power, gears help robotic joints execute exact movements, ensuring that robots can handle tasks that demand precision.
Robotic arms, for example, rely on a combination of motors and gears to achieve precise movements. Without gears, these arms would lack the ability to move with the fine control required for tasks like welding, soldering, or even painting.
Gears and Load Management in Robotics
Another important function of gears in robotic joints is load management. Robotic systems often need to handle heavy loads, especially in industries like automotive manufacturing, where robots are tasked with lifting and assembling heavy components. Gears play a critical role by enabling robots to bear large loads without losing control or precision.
Gears achieve this by distributing the load across the system. Planetary gear systems, for example, are designed to handle high torque, making them ideal for load-bearing applications in robotic arms or legs. By distributing the load more evenly, gears ensure that robots can perform tasks efficiently without putting too much strain on any single component.
Materials Used in Robotic Gears
The materials used to manufacture gears are another crucial factor that affects the performance of robotic joints. Common materials for gears include steel, brass, and composite materials, each with its own advantages.
- Steel gears are often used for heavy-duty applications because of their strength and durability. However, they can be heavy and create noise during operation.
- Brass gears are used in applications requiring low friction and quieter operation, though they may not be as durable as steel.
- Composite gears are lightweight and provide a balance between strength and smooth operation, making them ideal for precision-based robotic applications.
Choosing the right gear material can significantly impact the efficiency, durability, and precision of a robotic system.
Optimizing Gear Design for Robotic Applications
The design of gears used in robotic joints needs to be optimized for the specific task at hand. For example, gears in industrial robots are often designed to handle higher torque and loads, whereas gears in surgical robots require extreme precision and smoothness. Gear design also impacts the noise and vibration produced by the robotic system, which can affect the system’s performance and longevity.
Design Considerations:
- Size and weight: Lighter gears are more suitable for high-speed applications.
- Teeth shape and size: These factors affect how smoothly gears engage and transfer power.
- Lubrication: Proper lubrication is essential to minimize wear and ensure smooth operation.
An optimal gear design not only improves the overall performance of the robot but also extends its lifespan by reducing wear and tear.
Advances in Gear Technology for Robotics
Recent advances in gear technology are pushing the boundaries of what robots can achieve. Additive manufacturing (3D printing) allows for the creation of customized gears with complex designs that would be difficult to produce using traditional manufacturing techniques. These gears can be lighter, stronger, and more efficient, enabling robots to perform even more demanding tasks.
Additionally, advances in materials science have led to the development of self-lubricating gears, which reduce the need for maintenance and improve the reliability of robotic systems. This is especially useful in environments where robots need to operate continuously for long periods.
The Future of Gear Technology in Robotics
As robotics continues to evolve, the role of gear technology will become even more critical. The demands placed on robotic systems are increasing, with industries requiring robots to be faster, more precise, and more efficient than ever before. Gears are at the heart of this evolution, enabling robots to achieve higher levels of performance while maintaining reliability.
The development of more advanced gear materials, innovative designs, and manufacturing techniques will continue to push the capabilities of robots. Whether in industrial automation, healthcare, or aerospace, the importance of gears in robotic joints will remain central to the success of these systems.
Optimizing gear technology not only enhances the performance of robotic joints but also opens up new possibilities for what robots can achieve in the future.
By strategically incorporating keywords like gear technology in robotics, robotic joints, and precision gear systems into your content, you can improve the SEO visibility of your website. With keywords in the page title, subheadings, body content, and alt text for images, your website will have a greater chance of ranking higher in search engine results.