The Future of Gear Manufacturing: 3D Printing of Gears
3D printing, also known as additive manufacturing, is revolutionizing various industries, including the production of gears. This advanced manufacturing technology allows for the creation of complex and custom gear designs with precision and efficiency. The process involves layer-by-layer fabrication, which reduces waste and enables rapid prototyping. As 3D printing technology advances, it promises to significantly […]
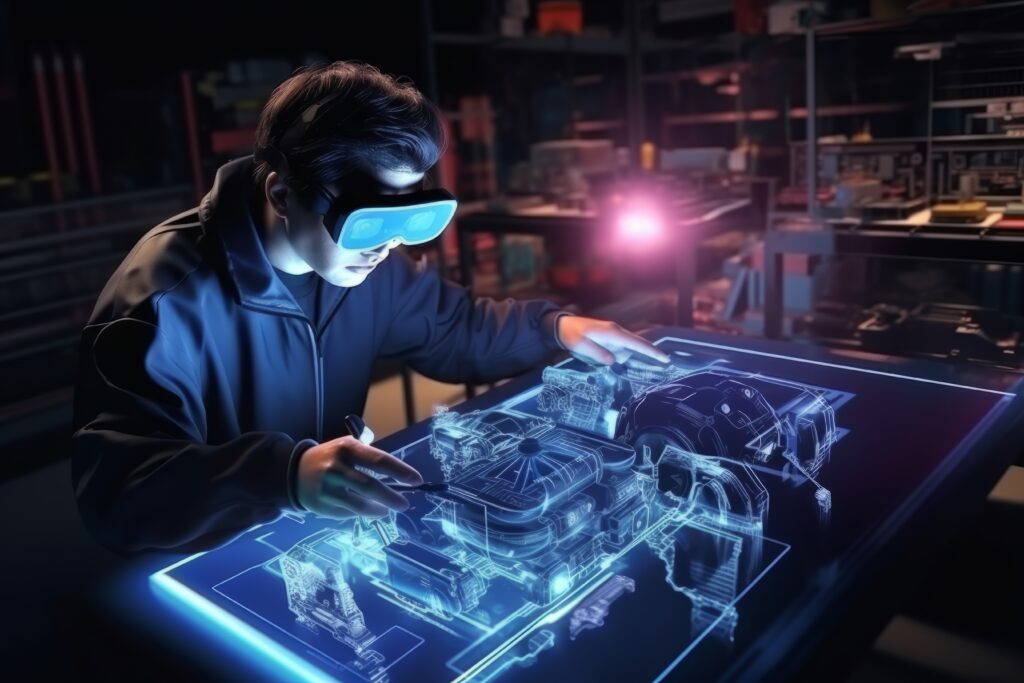
3D printing, also known as additive manufacturing, is revolutionizing various industries, including the production of gears.
This advanced manufacturing technology allows for the creation of complex and custom gear designs with precision and efficiency.
The process involves layer-by-layer fabrication, which reduces waste and enables rapid prototyping. As 3D printing technology advances, it promises to significantly impact the gear manufacturing industry by offering cost-effective, customizable, and highly accurate solutions.
The Evolution of Gear Manufacturing
Traditional gear manufacturing methods, such as hobbing, grinding, and milling, have been the standard for decades.
These processes, while effective, have limitations in terms of design flexibility, material waste, and production time. With the advent of 3D printing, these limitations are being addressed, ushering in a new era of gear manufacturing technology.
3D Printing and Additive Manufacturing
3D printing, or additive manufacturing, involves creating a three-dimensional object by adding material layer by layer, based on a digital model. This process contrasts with traditional subtractive manufacturing methods, which involve cutting away material from a solid block.
The ability to add material precisely where it is needed allows for the creation of intricate designs that would be challenging or impossible to achieve with conventional methods.
Advantages of 3D Printing for Gear Manufacturing: Design Flexibility and Customization
One of the most significant advantages of 3D printing in gear manufacturing is the ability to produce complex and custom gear designs. Traditional manufacturing techniques often restrict design possibilities due to tool limitations and machining constraints.
However, 3D printing allows engineers to explore innovative gear designs that optimize performance and meet specific application requirements. Custom gears can be tailored to precise specifications, enhancing their functionality and efficiency.
Precision and Accuracy
3D printing technology has advanced to the point where it can produce precision gears with high accuracy.
The layer-by-layer fabrication process ensures that each gear tooth is formed exactly as intended, reducing the risk of errors and deviations. This precision is crucial for gears that operate in high-performance applications, where even minor inaccuracies can lead to significant issues.
Rapid Prototyping
Another key benefit of 3D printing is the ability to rapidly prototype new gear designs. Traditional prototyping methods can be time-consuming and expensive, often requiring the production of molds and tooling. With 3D printing, prototypes can be created quickly and cost-effectively, allowing engineers to test and refine their designs in a fraction of the time.
This rapid prototyping capability accelerates the development process and enables faster innovation.
Material Efficiency
3D printing is inherently more material-efficient than traditional manufacturing methods. Because the process involves adding material only where it is needed, waste is minimized. This efficiency not only reduces costs but also has environmental benefits by conserving raw materials and reducing the overall carbon footprint of gear production.
Innovative Gear Materials
The flexibility of 3D printing extends to the types of materials that can be used in gear production. Traditional gears are typically made from metals such as steel and aluminum, which offer strength and durability but can be challenging to work with in complex designs.
3D printing opens the door to a wider range of materials, including advanced composites and polymers, which can be engineered to provide specific properties such as reduced weight, increased wear resistance, and enhanced lubrication.
Metal 3D Printing
Metal 3D printing technologies, such as selective laser melting (SLM) and electron beam melting (EBM), allow for the production of high-strength metal gears. These methods use a laser or electron beam to fuse metal powder into solid parts, layer by layer.
Metal 3D printing is particularly beneficial for producing custom gears with complex geometries that require the strength and durability of traditional metal gears.
Polymer and Composite Gears
Polymers and composites are increasingly being used in 3D-printed gears for applications where weight reduction and self-lubricating properties are desirable. Advanced polymers such as nylon, PEEK (polyether ether ketone), and carbon-fiber-reinforced composites offer excellent mechanical properties and can be printed with high precision. These materials are ideal for producing custom gears for applications in aerospace, automotive, and robotics.
Challenges and Considerations
While 3D printing offers numerous advantages for gear manufacturing, it also presents some challenges that need to be addressed. These include material limitations, post-processing requirements, and quality control.
Material Limitations
Not all materials are suitable for 3D printing, and the properties of 3D-printed materials can differ from those of traditionally manufactured materials. For example, 3D-printed metals may have different microstructures and mechanical properties due to the layer-by-layer fabrication process. It is essential to understand these differences and select appropriate materials for specific gear applications.
Post-Processing Requirements
3D-printed gears often require post-processing to achieve the desired surface finish and mechanical properties. This can include processes such as heat treatment, machining, and polishing. While 3D printing can produce complex geometries, achieving the same level of surface quality as traditional manufacturing methods may require additional steps.
Quality Control
Ensuring the quality and consistency of 3D-printed gears is crucial, especially for high-performance applications. This involves rigorous testing and inspection to detect any defects or variations in the printed parts. Advances in 3D printing technology are improving the reliability and repeatability of the process, but quality control remains a critical consideration.
Future Trends in 3D Printing of Gears
As 3D printing technology continues to evolve, several trends are emerging that will shape the future of gear manufacturing.
Multi-Material Printing
Multi-material 3D printing is an emerging technology that allows for the creation of gears with different materials in a single print. This capability enables the production of gears with customized properties, such as hard-wearing surfaces and lightweight cores. Multi-material printing opens up new possibilities for innovative gear designs that optimize performance and efficiency.
Integration with Digital Manufacturing
The integration of 3D printing with digital manufacturing technologies, such as computer-aided design (CAD) and computer-aided manufacturing (CAM), is streamlining the gear production process. Advanced software tools enable engineers to design, simulate, and optimize gear geometries before printing, reducing the need for physical prototypes and accelerating development cycles.
Automation and Production Scalability
Automation is playing a significant role in making 3D printing a viable option for large-scale gear production. Automated systems for material handling, post-processing, and quality inspection are being developed to increase the efficiency and scalability of 3D printing operations.
As these technologies mature, 3D printing will become more competitive with traditional manufacturing methods in terms of production volume and cost.
The future of gear manufacturing is being shaped by the advancements in 3D printing technology. The ability to produce complex, custom gears with high precision and material efficiency is transforming the industry.
While challenges remain, the benefits of 3D printing, such as design flexibility, rapid prototyping, and innovative materials, are driving its adoption in gear manufacturing. As technology continues to evolve,
3D printing will play an increasingly important role in producing the precision gears needed for a wide range of applications, from automotive and aerospace to robotics and industrial machinery.
The future of gear manufacturing is undoubtedly exciting, with 3D printing at the forefront of innovation and efficiency.