Revolutionizing Industries with 3D Gear Technology
Revolutionary Advances in 3D Gear Technology Transforming Industries 3D gear technology is transforming the way we design and manufacture gears. This innovative approach leverages advanced techniques to create precise, durable, and efficient gears, which are essential components in various industries. From automotive to aerospace, the applications of 3D gear technology are vast and ever-expanding. Understanding […]
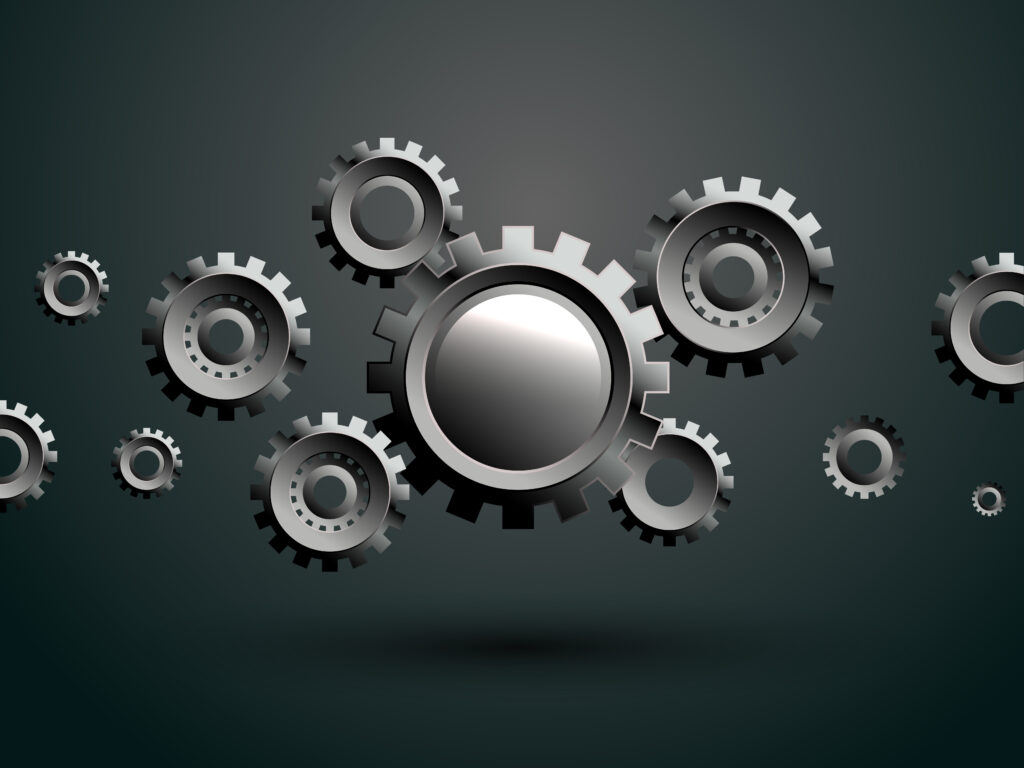
Revolutionary Advances in 3D Gear Technology Transforming Industries
3D gear technology is transforming the way we design and manufacture gears. This innovative approach leverages advanced techniques to create precise, durable, and efficient gears, which are essential components in various industries. From automotive to aerospace, the applications of 3D gear technology are vast and ever-expanding.
Understanding 3D Gear Technology
What is 3D Gear Technology?
3D gear technology refers to the use of additive manufacturing, also known as 3D printing, to produce gears. Unlike traditional manufacturing methods, which involve cutting away material, 3D printing builds up the gear layer by layer. This allows for greater design flexibility and precision.
Image Courtesy: Freepik
Benefits of 3D Gear Technology
The advantages of 3D gear technology are numerous. One of the most significant benefits is the ability to produce complex geometries that would be impossible or cost-prohibitive with traditional methods. Additionally, 3D printing reduces waste and can lead to faster production times.
Key Industries Benefiting from 3D Gear Technology
Several industries are already taking advantage of 3D gear technology. In the automotive industry, for instance, 3D-printed gears are used to create lighter and more fuel-efficient vehicles. The aerospace sector benefits from the technology’s ability to produce parts with intricate designs and high precision.
Advancements in 3D Gear Design
Customization and Flexibility
One of the standout features of 3D gear technology is customization. Manufacturers can easily adjust the design of gears to meet specific requirements. This flexibility leads to better performance and efficiency in machinery.
- Material Innovation
3D gear technology has also led to innovations in materials. Researchers are constantly developing new materials that offer improved strength, durability, and heat resistance. These materials are crucial for gears used in high-stress environments.
Cost-Effectiveness
While the initial investment in 3D printing technology can be high, the long-term cost savings are substantial. 3D gear technology reduces material waste and production time, leading to lower overall costs.
Challenges and Solutions in 3D Gear Manufacturing
Overcoming Design Limitations
Despite its many benefits, 3D gear technology does have some limitations. Complex designs can sometimes lead to structural weaknesses. However, ongoing research and development are addressing these challenges by improving design software and materials.
Ensuring Quality and Precision
Quality control is another challenge in 3D gear manufacturing. It is essential to ensure that the gears meet strict industry standards. Advanced software and precision machines help manufacturers maintain high-quality production.
Scaling Up Production
Scaling up production is another hurdle for 3D gear manufacturers. While 3D printing is ideal for small-batch production, it can be challenging to mass-produce gears quickly. Innovations in printer technology and production techniques are helping to address this issue.
The Future of 3D Gear Technology
Integration with IoT and AI
The future of 3D gear technology looks promising, especially with the integration of the Internet of Things (IoT) and artificial intelligence (AI). These technologies can optimize the design and production process, leading to even greater efficiency and precision.
Expanding Applications
As 3D gear technology continues to evolve, its applications will expand into new industries. Medical devices, consumer electronics, and renewable energy are just a few areas where 3D-printed gears could make a significant impact.
Sustainability and Environmental Impact
3D gear technology also has the potential to contribute to sustainability efforts. By reducing waste and energy consumption, 3D printing can help industries lower their carbon footprint and move towards more environmentally friendly practices.
Key Considerations for Adopting 3D Gear Technology
Assessing Compatibility
Before adopting 3D gear technology, companies should assess the compatibility of 3D printing with their existing processes. This involves evaluating the design and production needs of their products.
Training and Skill Development
Implementing 3D gear technology requires specialized skills and knowledge. Companies need to invest in training their workforce to effectively use and maintain 3D printing equipment.
Evaluating Return on Investment
While 3D gear technology offers numerous benefits, it is crucial to evaluate the potential return on investment (ROI). Companies should consider the long-term savings and advantages before making the transition.
The Impact of 3D Gear Technology
3D gear technology is revolutionizing industries by offering innovative solutions to complex manufacturing challenges. Its ability to produce precise, customized gears with minimal waste is transforming how companies approach design and production.
As technology continues to advance, the impact of 3D gear technology will only grow, leading to more efficient and sustainable manufacturing processes.