Radial Gears and Their Role in Cylindrical Gear Systems
Radial Gears in Cylindrical Gear Systems for Efficient Motion Understanding Radial Gears and Their Role in Cylindrical Drives Radial gears play a crucial role in cylindrical gear systems, where they ensure smooth and efficient transmission of motion. These gears are essential components in mechanical drives, helping transfer power with precision. Cylindrical gear systems rely on […]
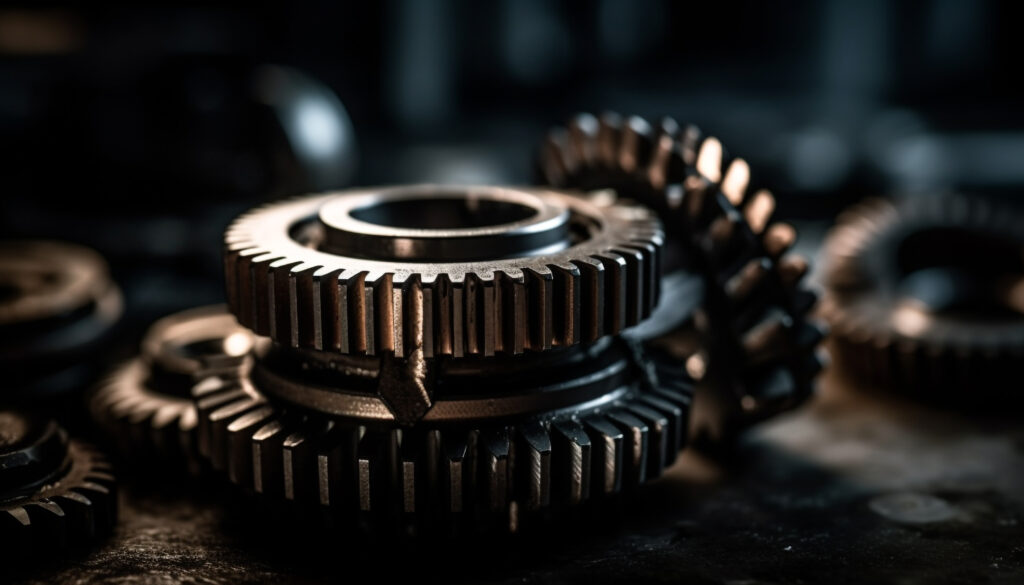
Radial Gears in Cylindrical Gear Systems for Efficient Motion
Understanding Radial Gears and Their Role in Cylindrical Drives
Radial gears play a crucial role in cylindrical gear systems, where they ensure smooth and efficient transmission of motion. These gears are essential components in mechanical drives, helping transfer power with precision. Cylindrical gear systems rely on the intermeshing of gears, and the design of radial gears ensures that this motion transfer is both smooth and effective.
Radial gears, unlike their counterparts in bevel or helical gear systems, have teeth aligned parallel to the axis of rotation, making them ideal for high-torque applications. In this article, we will delve into the functionality, importance, and applications of radial gears in cylindrical drives, explaining how they enhance machinery efficiency.
What Are Radial Gears?: Key Features of Radial Gears in Mechanical Systems
Radial gears are circular gears with teeth that project radially from the center of the gear body. Their primary function is to transmit torque and motion efficiently between rotating shafts in a cylindrical drive system. These gears operate by engaging with other radial gears, where the meshing of the teeth ensures a consistent transmission of force.
Key features of radial gears include:
- Straight Teeth: Unlike helical gears, radial gears have straight teeth that run parallel to the gear’s axis.
- High Torque Capacity: Radial gears are particularly suited for high-torque applications, making them ideal for heavy machinery.
- Smooth Power Transmission: Their design allows for smooth and reliable transmission of motion in cylindrical drives, with minimal loss of power.
These features make radial gears vital components in systems that require precise and reliable motion transfer, such as conveyor belts, automotive systems, and industrial machinery.
The Importance of Radial Gears in Cylindrical Drives : How Radial Gears Ensure Efficiency in Motion Transmission
In cylindrical gear systems, radial gears are essential for ensuring the proper engagement and transmission of force. Their ability to maintain a constant velocity ratio between gears helps reduce friction and wear, which is crucial for long-term machinery performance.
Advantages of radial gears in cylindrical drives:
- Efficient Power Transmission: Radial gears provide efficient motion transfer with minimal energy loss, ensuring machinery operates at optimal performance levels.
- Durability and Longevity: Due to their robust design, radial gears offer high durability, ensuring that the gear systems can handle heavy loads without excessive wear.
- Reduced Maintenance Costs: The efficient and smooth transmission of force provided by radial gears helps reduce the strain on the system, leading to fewer maintenance requirements over time.
This makes radial gears ideal for industries where uninterrupted operations are critical, such as manufacturing plants and heavy-duty machinery environments.
How Radial Gears Operate in Cylindrical Gear Systems : The Mechanics of Radial Gears in Motion Transfer
The working principle of radial gears in cylindrical drives revolves around the transfer of torque and rotational motion between shafts. In cylindrical gear systems, radial gears interlock with each other, allowing for the direct transmission of power.
When the teeth of radial gears engage, they mesh seamlessly to transmit rotational motion from one gear to another. The smooth engagement ensures that there is no slippage, making radial gears reliable for systems that require continuous and accurate motion transfer.
How this operation benefits machinery:
- Consistent Speed Ratio: Radial gears maintain a constant speed ratio, ensuring that machinery operates smoothly without sudden changes in speed or torque.
- High Load Capacity: Due to their design, radial gears can handle substantial loads without deforming, making them ideal for heavy-duty applications.
In cylindrical gear systems, this consistent speed and load handling capability are vital for ensuring that machinery operates efficiently under varying conditions.
Applications of Radial Gears in Industry : Where Radial Gears Are Used in Cylindrical Drives
Radial gears are found in a wide range of industrial applications, thanks to their ability to transfer motion efficiently in cylindrical drives. Their versatility makes them indispensable in various mechanical systems.
Common applications of radial gears include:
- Automotive Transmissions: Radial gears play a significant role in transferring power from the engine to the wheels, ensuring smooth acceleration and deceleration.
- Conveyor Systems: In conveyor belts, radial gears help maintain consistent motion, ensuring that products are transported efficiently along the assembly line.
- Industrial Machinery: Heavy-duty machinery such as presses and drills rely on radial gears to provide consistent torque and rotation, enabling precise operation.
Each of these applications benefits from the high torque capacity, durability, and efficiency that radial gears bring to cylindrical gear systems.
Optimizing Radial Gears for Maximum Efficiency : Enhancing the Performance of Radial Gears in Machinery
To maximize the efficiency of radial gears in cylindrical drives, certain factors must be considered during the design and implementation stages. Proper optimization of these gears can greatly improve the overall performance of the machinery.
Key factors for optimizing radial gear performance include:
- Material Selection: Choosing the right material for radial gears is crucial. High-strength alloys or composite materials can improve durability and reduce wear.
- Precision Manufacturing: The accuracy of the teeth on radial gears affects how well they mesh with other gears. High-precision manufacturing techniques ensure that the gear teeth are uniform and aligned properly.
- Lubrication: Proper lubrication is essential for reducing friction between radial gears and prolonging their operational life. Using high-quality lubricants helps minimize wear and maintain efficient motion transfer.
By focusing on these optimization techniques, machinery operators can ensure that radial gears perform at their best, reducing downtime and improving overall system efficiency.
Comparing Radial and Helical Gears : Why Choose Radial Gears Over Helical Gears?
While radial gears and helical gears are both used in cylindrical drives, they have distinct differences in design and application.
Comparison Table: Radial vs. Helical Gears
Feature |
Radial Gears |
Helical Gears |
Tooth Design |
Straight, parallel to the axis |
Angled, inclined to the axis |
Load Capacity |
High load capacity, ideal for torque | Moderate load capacity |
Noise Levels |
Low to moderate, depending on application | Quieter due to smoother engagement |
Friction |
Minimal friction |
More friction due to sliding action |
Efficiency |
High efficiency in straight engagement | Slightly lower due to sliding motion |
In comparison, radial gears are better suited for applications requiring high torque and efficiency, while helical gears are often preferred for quieter operation in applications where noise reduction is a priority.
Maintenance and Care for Radial Gears : Extending the Life of Radial Gears in Cylindrical Drives
Proper maintenance is essential for ensuring the long-term performance of radial gears in cylindrical systems. Without regular care, gears can wear down over time, leading to inefficiency and increased costs.
Key maintenance practices include:
- Regular Inspections: Regular visual inspections of the gear teeth help identify signs of wear or damage early on, preventing more extensive issues later.
- Lubrication Management: Ensuring that radial gears are properly lubricated at all times is crucial for reducing friction and preventing excessive wear. Always use the appropriate type of lubricant for your specific gear system.
- Alignment Checks: Misalignment between radial gears can lead to uneven wear and increased friction. Regular alignment checks ensure that the gears are meshing correctly, preventing unnecessary strain on the system.
By implementing these maintenance practices, you can significantly extend the lifespan of radial gears and ensure that your machinery operates efficiently.
Conclusion: The Importance of Radial Gears in Efficient Cylindrical Drives
Radial gears are essential components in cylindrical gear systems, providing smooth and efficient motion transmission in a variety of industrial applications. From automotive systems to heavy-duty industrial machinery, radial gears ensure that power is transferred reliably and with minimal energy loss.
Optimizing and maintaining radial gears is crucial for maximizing their performance. By selecting the right materials, ensuring precision manufacturing, and following regular maintenance practices, machinery operators can enhance the efficiency and lifespan of their systems.
As cylindrical gear systems continue to play a critical role in modern industry, radial gears remain at the forefront of innovation, ensuring that machinery operates at peak efficiency.