Non-Circular Gears: Versatile Solutions for Various Industries
The Role of Non-Circular Gears in Various Industrial Applications Non-circular gears, including elliptical, triangular, square, and other specialized forms, play a vital role in various industries. Their unique mechanical properties allow them to solve complex engineering challenges that traditional circular gears cannot. Used in applications like light industrial machines, military equipment, machine tools, and continuously […]
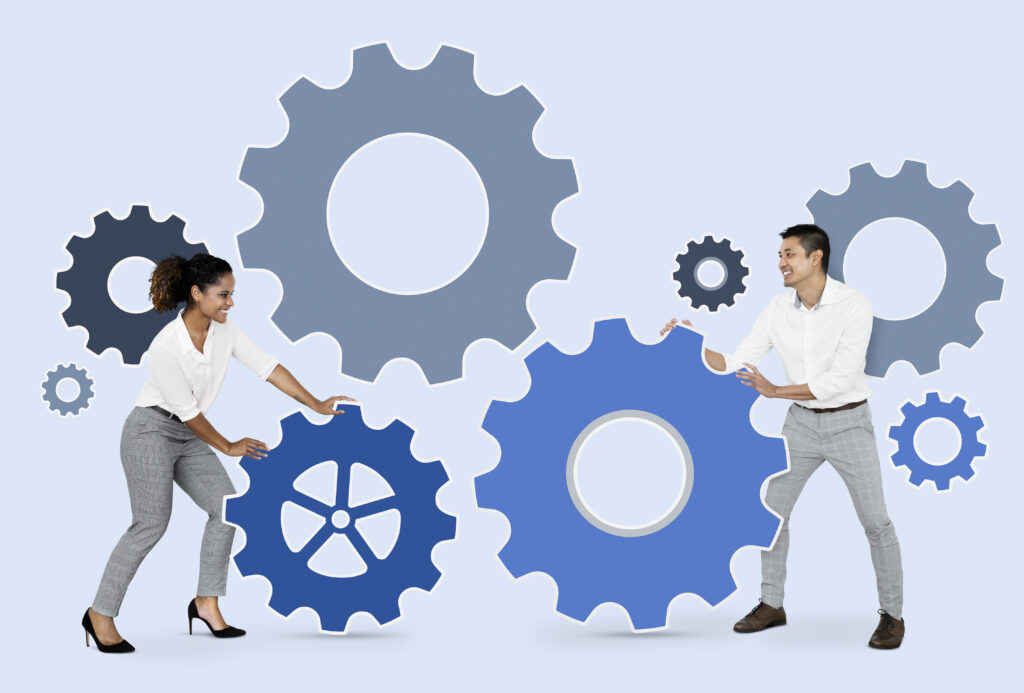
The Role of Non-Circular Gears in Various Industrial Applications
Non-circular gears, including elliptical, triangular, square, and other specialized forms, play a vital role in various industries. Their unique mechanical properties allow them to solve complex engineering challenges that traditional circular gears cannot. Used in applications like light industrial machines, military equipment, machine tools, and continuously variable transmissions (CVTs), non-circular gears provide precise, efficient performance. This article explores the types, functions, and key benefits of non-circular gears across diverse industries.
Understanding Non-Circular Gears
What Are Non-Circular Gears?
Non-circular gears are gears that deviate from the traditional circular form. These specialized gears are designed to achieve specific mechanical advantages, like controlling rotational speed, torque, or force at different points in their cycle. Engineers use these gears to tackle tasks that circular gears are inefficient at handling.
Image Courtesy: Freepik
Types of Non-Circular Gears
- Elliptical Gears
Elliptical gears provide variable speed and torque outputs. This makes them ideal for textile machines, where adjusting thread tension and speed is crucial for high-quality fabric production. - Triangular Gears
Triangular gears are used in applications requiring pulsating motion or specific timing sequences. Military equipment, such as weapon systems, often relies on these gears for their precision. - Square Gears
These gears are designed for intermittent motion, often found in automated manufacturing and conveyor systems requiring precise start-stop mechanisms. - Multispeed Gears
Multispeed gears provide variable speed outputs, making them perfect for CVTs in automotive industries. They ensure smooth and efficient transitions between different operating speeds. - Eccentric Gears
With an off-center rotation, gears offer varying torque throughout their rotation. They are widely used in flow meters and hydraulic motors, where precise control is needed for fluid management. - Logarithmic Spiral Gears
These gears, shaped like a logarithmic spiral, maintain consistent speed changes during rotation. They are used in potentiometers and variable-speed windshield wipers. - Cam Gears
Cam gears are essential in converting rotational motion into linear motion, commonly used in automotive engines for precise timing of engine valves.
Applications of Non-Circular Gears
1. Light Industry Machinery
Non-circular gears play a key role in light industry machinery by offering variable speed and torque control. They are ideal for machines that handle packaging, assembly, and other automated tasks, enhancing precision and efficiency.
2. Textile Machines
Elliptical and triangular gears are instrumental in controlling thread tension and speed in textile machines. This ensures consistent fabric quality and minimizes machine wear, contributing to higher productivity.
3. Machine Tools
Machine tools benefit from multispeed and eccentric gears that allow for precise tool movement and speed adjustments. This precision is critical for achieving the desired accuracy in manufactured parts.
4. Military Applications
In military applications, non-circular gears such as cam gears provide critical precision and timing. These gears are used in weapon systems and radar equipment, ensuring reliability in harsh environments.
5. Potentiometers
Elliptical and logarithmic spiral gears are commonly used in potentiometers, devices that measure electrical potential. These gears allow for smooth and precise resistance adjustments in electronic devices.
6. Continuously Variable Transmissions (CVTs)
CVTs rely on non-circular gears for seamless speed transitions. Multispeed and eccentric gears in these systems provide smooth and efficient power delivery, which is essential for improving fuel efficiency in vehicles.
7. Positive and Negative Rotation Mechanisms
In robotics and automation systems, non-circular gears provide precise control over bidirectional movements. This enhances the responsiveness and accuracy of robotic systems.
8. Flow Meters
Flow meters use eccentric and logarithmic spiral gears to manage the flow rate of liquids and gases. These gears ensure accurate readings, which are critical in industrial processes and environmental monitoring.
9. Hydraulic Motors
Hydraulic motors, which convert fluid power into mechanical motion, benefit from non-circular gears that offer variable torque and speed, improving the overall efficiency of hydraulic systems.
10. Sprockets
Square and triangular gears are used in sprockets to achieve precise motion control in conveyor systems. These gears provide intermittent and pulsating motions necessary for material handling.
11. Variable-Speed Windshield Wipers
Elliptical and cam gears in windshield wipers ensure smooth and responsive operation based on the driver’s settings, enhancing visibility and safety in various weather conditions.
Benefits of Non-Circular Gears
1. Enhanced Performance
Non-circular gears provide variable speed and torque characteristics, which lead to more efficient machine operation. This adaptability improves control over mechanical processes.
2. Improved Precision
The ability of non-circular gears to offer precise control over motion makes them ideal for applications requiring exact timing, such as military equipment and automotive systems.
3. Versatility
These gears are suitable for a wide range of industries, including textile, military, and light industrial machinery, offering solutions to unique mechanical challenges.
4. Efficiency
By optimizing speed and torque, non-circular gears improve energy efficiency and reduce wear on machinery components, resulting in longer-lasting equipment.
5. Innovation
The ability of non-circular gears to perform functions that circular gears cannot opens up new possibilities in mechanical design, promoting further technological advancements.
Non-circular gears are revolutionizing industries with their specialized designs and versatile applications. Their ability to enhance efficiency, precision, and performance makes them indispensable in modern engineering. From light industrial machinery to military systems, non-circular gears are pushing the boundaries of what mechanical systems can achieve. As industries continue to evolve, the demand for innovative solutions like non-circular gears will only grow, paving the way for further advancements in technology.