Machinery Work holding: The Key to Successful Gear Machining
Optimizing Machinery Work holding for Precise Gear Machining Why Machinery Work holding is Crucial for Gear Machining The success of gear machining is heavily dependent on one critical factor—machinery work holding. In any machining process, ensuring that a gear is securely and accurately held in place is crucial for achieving precision and avoiding errors. Without […]
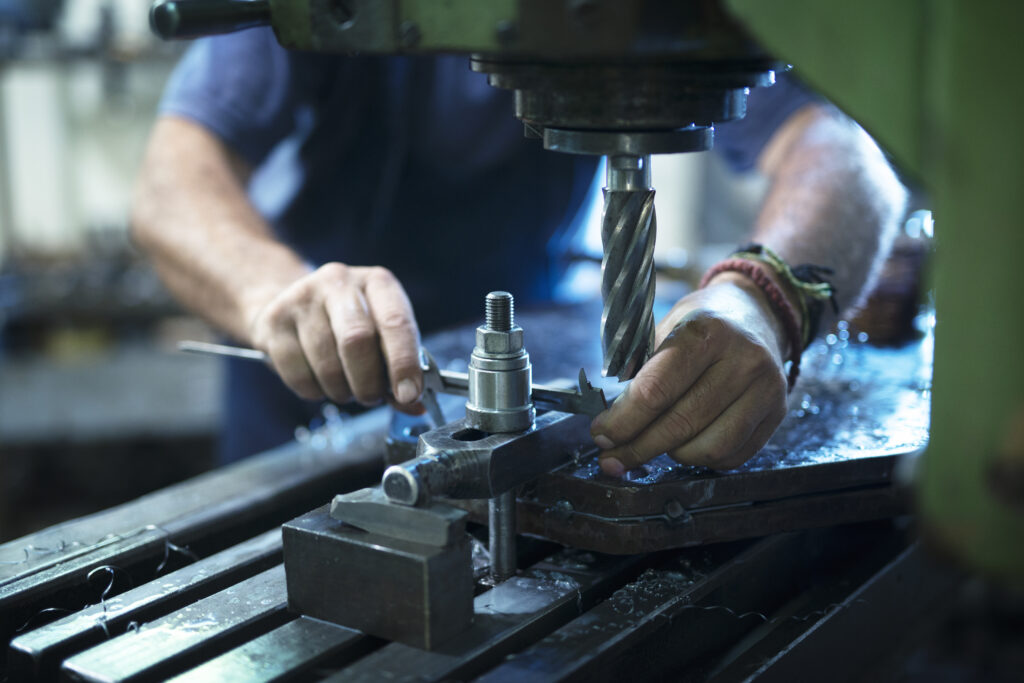
Optimizing Machinery Work holding for Precise Gear Machining
Why Machinery Work holding is Crucial for Gear Machining
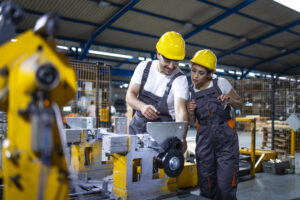
The success of gear machining is heavily dependent on one critical factor—machinery work holding. In any machining process, ensuring that a gear is securely and accurately held in place is crucial for achieving precision and avoiding errors. Without proper work holding, gears may shift during machining, leading to misaligned cuts, material waste, and costly production delays.
Machinery work holding systems are designed to prevent these issues by securing the work piece in place, ensuring it remains stationary throughout the machining process. This not only improves the quality of the finished gear but also enhances overall machining efficiency.
The following article will explore how different machinery work holding systems contribute to successful gear machining, with insights into best practices that improve gear production outcomes.
Understanding Machinery Work holding Systems for Gears
In gear machining, the importance of machinery work holding cannot be overstated. The precision of every cut and finish depends on how firmly the work piece is secured during the machining process. But what exactly is work holding in machinery, and why is it so crucial in gear production?
Work holding refers to the devices and techniques used to hold a gear, or any other component, in place during machining. Common machinery work holding systems include chucks, vises, clamps, and fixtures, each designed for specific gear types and machining methods. These systems are used to ensure that the gear remains stable and aligned, reducing the chance of human error or machine inaccuracies.
Key Components of a Work holding System :The Essential Parts of Gear Machining Work holding
A typical machinery work holding system involves several key components:
- Chucks: Often used in lathe machining, chucks are devices that hold the gear in place by clamping it tightly. They provide the rotational grip needed for precise turning operations.
- Vises: Vises are commonly used in milling machines and other static machining processes. They hold the gear in a fixed position, allowing for accurate, static cuts.
- Clamps: Clamps secure the gear in place during milling or grinding processes. Clamps must be strong enough to prevent any movement but not so tight that they damage the gear.
- Fixtures: Fixtures are customized work holding devices that are specifically designed for a particular gear or work piece. These are used for high-precision machining when standard chucks or vises are inadequate.
By using the right work holding system, manufacturers can improve the machining gear process, making it more efficient and reliable.
The Role of Work holding in Gear Accuracy : Achieving Precision in Gear Machining
One of the most critical factors in gear machining is ensuring that each cut is precise. Work holding machinery plays a pivotal role in achieving this precision by securing the gear in place, preventing any unwanted movement that could lead to errors.
When gears are properly held during machining, it is much easier to maintain tolerance levels and ensure that each gear tooth is accurately formed. This is particularly important in high-stakes industries like aerospace, automotive, and industrial automation, where even the smallest deviation in gear dimensions can lead to functional issues.
Work holding systems also reduce the likelihood of producing defective gears, which can save time and money by minimizing the need for rework or replacements.
Best Practices for Improving Gear Production Outcomes: How to Optimize Work holding for Gear Machining
To ensure successful gear machining, manufacturers must implement several best practices related to machinery work holding. These practices are designed to enhance gear accuracy, reduce production downtime, and improve overall operational efficiency. Here are some key tips:
- Select the Appropriate Work holding System: Depending on the gear type and machining method, select the correct work holding device. For turning operations, use chucks that provide a strong grip on rotational parts. For static processes, such as milling or grinding, opt for vises or clamps.
- Customize Work holding Fixtures: In cases where standard work holding devices are inadequate, custom fixtures should be designed to securely hold gears in place. Custom fixtures are especially useful for complex gear shapes or when high tolerances are required.
- Regular Maintenance and Calibration: Machinery work holding systems, like all tools, require regular maintenance. Calibration should be performed periodically to ensure the work holding devices remain accurate and reliable during gear machining.
- Test for Stability and Precision: Before proceeding with gear machining, always test the stability of the work holding system. Any movement, even slight, can affect the final product. Make adjustments to the work holding system if necessary to eliminate any potential instability.
- Use Intelligent Work holding Systems: Advanced CNC machines are now integrating intelligent work holding systems that automatically adjust during the machining process. These systems can optimize grip pressure and positioning based on the gear’s machining requirements, further reducing errors.
Table: Comparison of Work holding Devices in Gear Machining
Work holding Device |
Ideal Use | Advantages | Disadvantages |
Chucks |
Lathe Machining | Provides strong grip for rotating parts |
May require recalibration frequently |
Vises |
Milling and Grinding | Fixed, stable positioning for static processes | Limited flexibility |
Clamps |
General Machining | Easy to adjust and secure |
May not be suitable for high-precision work |
Fixtures |
Customized Machining | Perfect for complex gear shapes and high-precision needs | Can be expensive and time-consuming to design |
How Work holding Reduces Errors in Gear Machining :Minimizing Common Gear Machining Errors with Proper Work holding
Errors in gear machining can be costly, leading to material waste, production delays, and lower-quality products. However, by using proper work holding machinery, manufacturers can minimize these issues.
- Misalignment: One of the most common errors in gear machining is misalignment, where the gear shifts slightly during the machining process. This results in miscut teeth, making the gear unusable. Using the correct work holding system, such as a customized fixture or properly aligned chuck, can prevent this issue.
- Excessive Vibration: When a gear is not securely held in place, it can cause excessive vibration during machining. This vibration leads to poor surface finishes, irregular tooth profiles, and sometimes even tool breakage. Machinery work holding that properly secures the gear can reduce vibration and lead to better results.
- Human Error: Manual errors, such as improperly securing the gear in a vise or not tightening clamps sufficiently, can cause problems during machining. Using intelligent, automated work holding systems can eliminate these errors by ensuring that the gear is always properly positioned and secured.
Enhancing Efficiency in Gear Machining with Work holding Systems)
Proper machinery work holding not only improves precision but also increases machining efficiency. By securing the gear correctly from the start, manufacturers can reduce downtime caused by errors or the need for manual adjustments. This leads to a more streamlined machining process, allowing operators to focus on production rather than constantly checking and re-securing gears.
Moreover, intelligent work holding systems that automatically adjust based on the gear’s dimensions or the machining task can significantly reduce the need for operator intervention. These systems can detect any potential issues in real-time and make necessary adjustments, ensuring the machining process continues smoothly without any interruptions.
Machinery Work holding: The Key to Successful Gear Machining)
Machinery work holding is a critical component in ensuring the precision and success of gear machining. By using the appropriate work holding devices, whether chucks, vises, or customized fixtures, manufacturers can drastically reduce errors, improve gear accuracy, and enhance overall machining efficiency.
Adopting best practices like regular maintenance, testing for stability, and using advanced intelligent work holding systems ensures that your machining gear process remains smooth and error-free. Proper work holding is not only about securing the work piece; it is about improving production outcomes, saving time, and reducing costs.