Lubrication Strategies for Optimized Gear Technology
The Ultimate Guide to Gear Lubrication: Maximizing Performance and Longevity Lubrication is the lifeblood of gear technology, ensuring that mechanical systems run smoothly, efficiently, and with minimal wear and tear. Gears are fundamental components in a myriad of applications, from automotive transmissions and industrial machinery to wind turbines and aerospace technology. Proper lubrication is critical […]
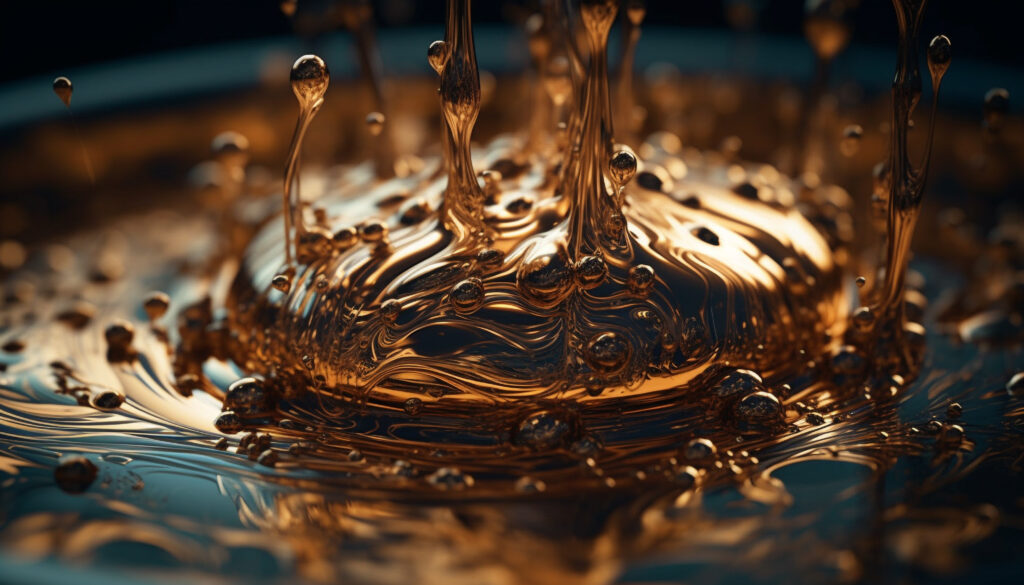
The Ultimate Guide to Gear Lubrication: Maximizing Performance and Longevity
Lubrication is the lifeblood of gear technology, ensuring that mechanical systems run smoothly, efficiently, and with minimal wear and tear.
Gears are fundamental components in a myriad of applications, from automotive transmissions and industrial machinery to wind turbines and aerospace technology. Proper lubrication is critical to maximizing the performance, reliability, and longevity of gear systems.
Importance of Lubrication in Gear Technology
Gears endure high loads and speeds, generating substantial friction and heat. Without proper lubrication, this friction causes severe wear, pitting, and potential gear failure.
Effective lubrication reduces friction, dissipates heat, prevents wear, protects against corrosion, and removes contaminants, ensuring the longevity and reliability of gear components.
Lubrication serves several crucial functions:
Reducing Friction efficiency : Lubricants play a pivotal role in reducing friction within gear systems. By forming a thin film between gear teeth, lubricants effectively separate the metal surfaces. This reduction in direct metal-to-metal contact significantly decreases friction.
Lower friction not only enhances the efficiency of the gear operation but also reduces the energy required to move the gears, leading to lower operating costs and improved overall performance.
Dissipating Heat
During operation, gears generate a considerable amount of heat due to friction. Lubricants are essential for carrying away this heat, preventing the gear system from overheating. By maintaining a stable operating temperature, lubricants help to preserve the mechanical properties of the gear materials and prevent thermal degradation.
Effective heat dissipation also minimizes the risk of thermal expansion and distortion of gear components, which can adversely affect performance and alignment.
Preventing Wear
Wear and tear are inevitable in any mechanical system, but lubricants can significantly mitigate these effects. By minimizing friction, lubricants reduce the wear on gear teeth, thereby extending the life of the gear components.
This is particularly important in high-load applications where the pressures on gear surfaces can be immense. Regular and proper lubrication ensures that gears operate smoothly over extended periods, reducing the frequency of maintenance and replacement.
Protecting Against Corrosion
Gears are often exposed to harsh environments that can lead to corrosion and rusting of metal surfaces. Lubricants typically contain additives designed to protect against corrosion. These additives form a protective barrier on the metal surfaces, preventing moisture and corrosive substances from causing damage.
This corrosion protection is crucial for maintaining the integrity and reliability of gear systems, especially in outdoor or marine environments where exposure to water and corrosive elements is common.
Contaminant Removal
During operation, gear systems can accumulate debris and contaminants, such as metal particles, dirt, and other foreign materials. Lubricants help to flush out these contaminants from the gear system.
By maintaining cleanliness, lubricants ensure that gears continue to operate efficiently and prevent abrasive particles from causing additional wear. Clean lubrication not only enhances the performance of the gear system but also extends the lifespan of both the lubricant and the gear components. Regular monitoring and replacement of lubricants are essential to maintaining this cleanliness and ensuring optimal gear operation.
Types of Lubricants for Gears
The choice of lubricant depends on the specific application and operating conditions of the gear system. There are several types of lubricants used in gear technology:
Mineral Oils
Derived from petroleum, mineral oils are the most commonly used lubricants in gear technology. They are favored for their cost-effectiveness and broad applicability across various industries. Mineral oils provide satisfactory performance in many gear applications due to their inherent lubricating properties.
However, they often require the addition of performance-enhancing additives such as anti-wear agents, rust inhibitors, and antioxidants to meet the demands of more strenuous operating conditions.
Despite their widespread use, mineral oils may have limitations in terms of thermal stability and oxidation resistance, making them less suitable for high-temperature or extreme pressure environments without significant additive enhancement.
Synthetic Oils
Synthetic oils are engineered lubricants designed to meet specific performance criteria that exceed the capabilities of mineral oils. Types of synthetic oils used in gear systems include polyalphaolefins (PAOs), esters, and polyalkylene glycols (PAGs).
These lubricants offer superior temperature stability, maintaining their viscosity and lubricating properties over a wide range of temperatures.
Additionally, synthetic oils exhibit excellent oxidation resistance, which prolongs the service life of the lubricant and reduces the frequency of oil changes. Their enhanced lubricating qualities ensure better protection against wear and tear, making them ideal for high-performance applications where reliability and longevity are critical.
Solid Lubricants
In certain applications where liquid lubricants may not perform adequately, solid lubricants such as graphite, molybdenum disulfide (MoS2), or polytetrafluoroethylene (PTFE) are utilized. These materials provide effective lubrication under extreme conditions, such as high temperatures, vacuum environments, or in the presence of reactive chemicals.
Solid lubricants can form a durable, low-friction layer on gear surfaces, reducing wear and maintaining smooth operation where conventional oils or greases might fail. Their use is often critical in aerospace, military, and other high-stress applications where liquid lubricants would evaporate, oxidize, or become ineffective.
Greases: Greases are a combination of base oil, thickener, and additives, providing a semi-solid lubricant that can stay in place better than liquid oils. This makes greases particularly useful in applications where lubricant retention is challenging, such as in open gears or vertical shafts.
The thickener matrix holds the base oil in place, allowing it to release under pressure and provide continuous lubrication. Greases offer excellent adhesion to surfaces, ensuring consistent protection against wear, even in high-load or low-speed conditions. They are also beneficial in preventing contamination ingress and maintaining lubrication in environments where re-lubrication intervals are longer or less accessible.
Methods of Lubrication
Various methods are employed to apply lubricants to gear systems, each suited to different operational needs and environments:
Splash Lubrication: Splash lubrication relies on the movement of the gears themselves to distribute the lubricant. As the gears rotate, they pick up lubricant from a reservoir and splash it onto all the internal surfaces.
This method is commonly used in enclosed gearboxes and is effective for moderate-speed applications. Splash lubrication is simple and requires minimal additional components, making it cost-effective and easy to maintain.
However, its effectiveness can be limited in high-speed or high-load conditions where more sophisticated lubrication methods may be necessary to ensure adequate coverage and cooling.
Circulating Oil Systems: In circulating oil systems, oil is continuously pumped through the gear system, providing a steady supply of fresh lubricant. This method ensures thorough lubrication of all components and effective removal of heat generated by friction.
Circulating systems are used in high-performance and high-load applications where precise temperature control and contamination management are critical. These systems often include filters to remove debris and contaminants from the oil, extending the service life of both the lubricant and the gear components.
The continuous flow of oil helps maintain optimal operating conditions, enhancing the reliability and efficiency of the gear system.
Mist Lubrication: Mist lubrication systems deliver lubricant in the form of a fine mist, ensuring even and minimal distribution across gear surfaces. This method is particularly useful in high-speed applications where traditional lubrication methods might fail to provide sufficient coverage without causing drag or excessive heat buildup.
Oil mist systems are designed to operate with very small quantities of lubricant, making them efficient and reducing the risk of over-lubrication. This method also helps in cooling the gear surfaces by evaporating quickly, taking heat away with the mist particles. Mist lubrication is commonly used in applications like high-speed bearings, turbines, and other precision machinery.
Grease Lubrication: For gear systems where liquid lubricants might leak or be difficult to contain, grease is often used. Grease provides a thick, sticky lubricant that adheres well to gear surfaces, making it suitable for open gears or systems operating at low speeds and high loads.
Grease can also act as a sealant, preventing the ingress of dirt and moisture, which could otherwise cause contamination and corrosion.
The viscosity of grease allows it to stay in place over long periods, providing consistent lubrication with less frequent reapplication compared to oils. This makes it ideal for applications where maintenance access is limited or infrequent.
Dry Lubrication: In extreme environments where traditional liquid lubricants are not viable, dry lubrication using solid lubricants or special coatings is employed.
These methods are particularly useful in high-temperature environments, such as furnaces or engines, and in vacuum conditions, like those found in space applications.
Solid lubricants like graphite and MoS2 provide low-friction, high-wear resistance under conditions where oils and greases would evaporate or degrade.
Special coatings can also be applied to gear surfaces to enhance their lubricating properties and extend their service life under harsh conditions. Dry lubrication ensures reliable operation in environments where other lubrication methods would fail.
Best Practices for Gear Lubrication
To ensure optimal performance and longevity of gear systems, it is essential to follow best practices in lubrication:
Regular Monitoring: Regularly monitoring the condition of the lubricant and the gear system is crucial for early detection of potential issues. Parameters such as viscosity, temperature, and contamination levels should be checked periodically.
Monitoring systems can provide real-time data, allowing for proactive maintenance and reducing the risk of unexpected failures. Regular oil analysis can identify changes in lubricant properties that indicate wear, contamination, or degradation, enabling timely corrective actions to maintain gear system health.
Proper Selection: Choosing the right type of lubricant based on the specific gear type, load, speed, and operating environment is essential. Consulting with lubricant manufacturers or specialists can provide valuable insights into the best lubricant for a given application. Factors such as temperature range, pressure, and exposure to contaminants must be considered.
Using the appropriate lubricant ensures optimal performance, minimizes wear, and extends the life of the gear system.
Maintaining Cleanliness: Maintaining the cleanliness of both the lubricant and the gear system is vital. Contaminants such as dirt, metal particles, and water can degrade the lubricant and cause damage to gear components. Regularly replacing filters and ensuring that the lubricant is free from contaminants can prevent abrasive wear and corrosion.
Clean lubrication systems reduce the risk of downtime and costly repairs, ensuring consistent and reliable gear operation.
Adequate Application: Applying the correct amount of lubricant is critical for effective gear lubrication. Too little lubricant can lead to inadequate protection and increased wear, while too much can cause overheating, energy loss, and potential lubricant breakdown.
Following manufacturer recommendations and using precise application methods ensures that the right amount of lubricant is delivered to critical areas. Proper application techniques help maintain the balance between lubrication efficiency and system performance.
Regular Replacement: Lubricants degrade over time due to oxidation, contamination, and thermal breakdown. Following the manufacturer’s recommendations for replacement intervals is essential to maintain optimal performance.
Regularly replacing the lubricant ensures that it retains its protective properties and continues to provide effective lubrication. Scheduled lubricant changes prevent the buildup of harmful contaminants and extend the life of both the lubricant and the gear components.
Using Additives: In some cases, additives can enhance the performance of lubricants. Anti-wear additives, corrosion inhibitors, and extreme pressure additives provide additional protection under specific conditions.
Selecting lubricants with the right additives can improve their performance in challenging environments. Additives enhance the lubricant’s ability to protect against wear, resist corrosion, and perform under extreme pressures, ensuring reliable gear operation even under demanding conditions.
Challenges and Future Trends
The field of gear lubrication is constantly evolving, driven by the need for higher performance, efficiency, and environmental considerations. Some of the challenges and future trends include:
Environmental Regulations: Stricter environmental regulations are pushing for the development of more eco-friendly lubricants. Biodegradable and non-toxic lubricants are becoming increasingly important as industries strive to reduce their environmental impact.
The development of lubricants that meet regulatory requirements while providing high performance is a growing area of focus. Eco-friendly lubricants reduce the risk of environmental contamination and improve sustainability in gear lubrication practices.
Advanced Materials: The development of new materials and coatings for gears may reduce the reliance on traditional lubricants. Self-lubricating materials and advanced surface treatments are areas of ongoing research.
These innovations aim to provide inherent lubricating properties, reducing the need for external lubrication and enhancing the durability of gear systems. Advanced materials and coatings can offer superior wear resistance, lower friction, and improved performance in extreme conditions, paving the way for more efficient and reliable gear systems.
Condition Monitoring: Advances in sensor technology and data analytics are enabling more precise condition monitoring and predictive maintenance. Real-time monitoring of lubricant condition and gear performance can help in early detection of issues and reduce downtime.
Condition monitoring systems provide valuable insights into the health of gear systems, allowing for timely maintenance and repairs. Predictive maintenance strategies improve operational efficiency, extend the life of gear components, and minimize unexpected failures.
Nano-lubricants: The use of nanotechnology in lubricants is an emerging trend. Nano-lubricants can offer enhanced properties such as reduced friction, better thermal stability, and improved wear resistance. Incorporating nanoparticles
Lubrication is a critical component in the successful operation of gear systems. By understanding the types of lubricants, methods of application, and best practices for maintenance, engineers and technicians can ensure that gear systems perform reliably and efficiently.
As technology advances, new materials, monitoring techniques, and sustainable practices will continue to shape the future of gear lubrication, driving improvements in performance and environmental impact.
In an ever-evolving field, staying informed about the latest trends and innovations is essential for anyone involved in gear technology. By prioritizing proper lubrication, we can maximize the life and performance of gear systems, ensuring their crucial role in various applications continues to be fulfilled effectively. continues to be fulfilled effectively.