Efficient and Reliable Gear Solutions for Optimal Performance
Discover Cutting-Edge Gear Technologies to Enhance Machinery Longevity In today’s fast-paced industrial landscape, the demand for efficient and reliable gear solutions has never been greater. Whether in automotive, manufacturing, or aerospace industries, gears play a crucial role in ensuring smooth and effective mechanical operations. This article explores the latest advancements in gear technology, the importance […]
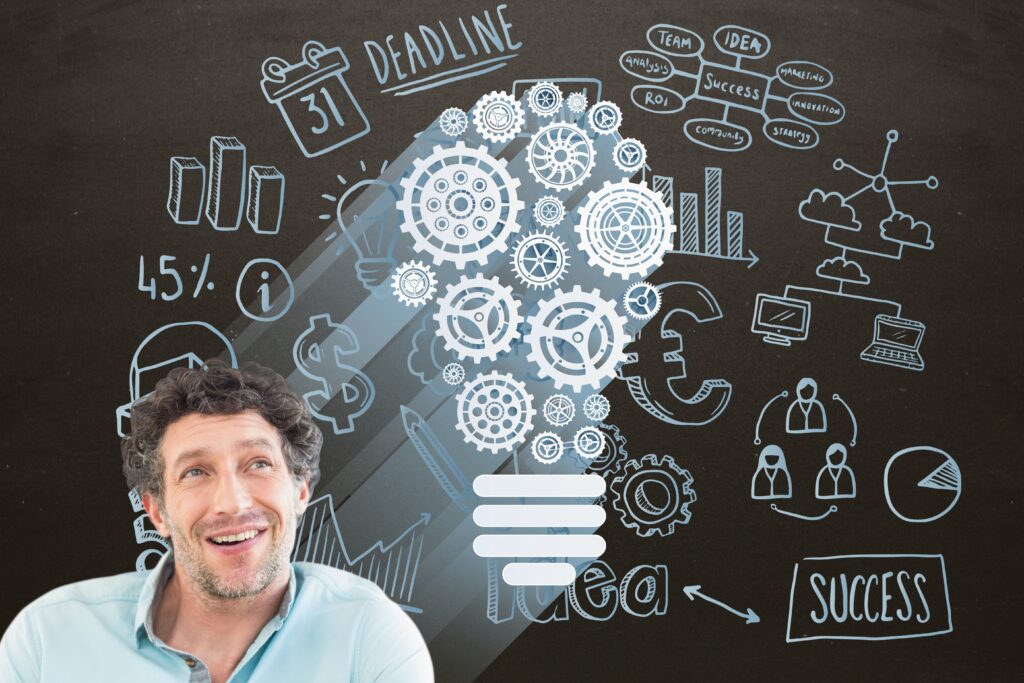
Discover Cutting-Edge Gear Technologies to Enhance Machinery Longevity
In today’s fast-paced industrial landscape, the demand for efficient and reliable gear solutions has never been greater. Whether in automotive, manufacturing, or aerospace industries, gears play a crucial role in ensuring smooth and effective mechanical operations.
This article explores the latest advancements in gear technology, the importance of choosing high-quality gear systems, and how they can improve performance and extend the lifespan of machinery.
The Role of Gears in Various Industries
Gears are integral to numerous industries. In automotive applications, they ensure efficient power transmission from the engine to the wheels. Manufacturing relies on gears for precision in machinery and assembly lines.
Aerospace utilizes high-quality gears for critical operations in engines and control systems, emphasizing the need for reliability and durability.
Advancements in Gear Technology- Latest Innovations in Gear Design and Materials
Recent years have seen significant advancements in gear design and materials. Innovative gear designs, such as herringbone gears, reduce noise and increase load capacity.
Advanced materials like carbon-fiber composites and high-strength alloys enhance mechanical efficiency and longevity. These materials provide greater resistance to wear and tear, reducing the frequency of replacements.
Impact of Technology on Gear Efficiency and Reliability
Technology has revolutionized gear manufacturing processes. Computer-Aided Design (CAD) and precision machining enable the production of gears with exact specifications, ensuring high efficiency and reliability. Additive manufacturing (3D printing) has introduced the possibility of creating complex gear shapes that were previously unattainable, further improving performance and reducing waste.
Choosing High-Quality Gear Systems
Criteria for Selecting Reliable Gears
Selecting high-quality gears involves considering several factors:
Material Quality: Opt for gears made from durable materials that can withstand high stress and wear.
Precision Manufacturing: Ensure the gears are produced with high precision to meet exact tolerances.
Reputable Manufacturer: Choose manufacturers with a proven track record of reliability and quality assurance.
Benefits of High-Quality Gears on Machine Performance
High-quality gears enhance machine performance by providing:
Greater Efficiency: Reduced friction and smoother operation increase overall efficiency.
Extended Lifespan: Durable materials and precise manufacturing result in longer-lasting gears.
Reduced Downtime: Reliable gear systems decrease the likelihood of mechanical failures, ensuring continuous operation.
Enhancing Gear Performance: Techniques and Strategies
Techniques for Optimizing Gear Performance
Optimizing gear performance involves several techniques to ensure efficiency and reliability:
Proper Lubrication: Proper lubrication is essential for smooth gear operation and reduced wear. Regularly check and replace lubricants as needed to maintain optimal performance.
Alignment: Correct gear alignment is crucial to prevent excessive wear and tear. Ensure gears are properly aligned to enhance their longevity and performance.
Load Distribution: Evenly distribute loads across gears to avoid overloading and potential damage. Proper load distribution minimizes stress and extends gear life.
The Importance of Proper Lubrication and Maintenance
Proper lubrication and maintenance are crucial for gear longevity and performance. Use high-quality lubricants suitable for specific gear types and operating conditions. Regular maintenance checks help identify potential issues early, preventing major failures and extending the life of the gear systems. Maintaining optimal lubrication and regular check-ups ensure gears operate smoothly and efficiently.
Extending the Lifespan of Gears
Implementing preventative maintenance strategies can significantly extend the lifespan of gears:
Routine Inspections: Regularly inspect gears for signs of wear, misalignment, and lubrication levels. Routine inspections help catch problems early, preventing severe damage.
Condition Monitoring: Use technologies like vibration analysis and thermography to monitor gear condition in real-time. These tools provide valuable insights into gear health, allowing for timely interventions.
Timely Repairs: Address minor issues promptly to prevent them from escalating into major problems. Timely repairs save costs and reduce downtime, ensuring continuous operation.
Identifying and Addressing Common Gear Issues includes:
Wear and Tear: Regular use can lead to gradual wear. Address this by replacing worn parts and using appropriate lubricants to minimize further damage.
Misalignment: Misalignment can cause uneven load distribution. Regularly check and adjust alignment to prevent excessive wear and operational issues.
Overheating: Ensure adequate cooling and lubrication to prevent overheating, which can degrade gear materials. Proper thermal management is essential for maintaining gear integrity.
Customized gear solutions offer several advantages:
Specific Fit: Tailor-made gears fit perfectly into specific applications, ensuring optimal performance. Custom gears are designed to meet unique operational requirements.
Enhanced Efficiency: Customized designs can be optimized for particular load and speed requirements, enhancing overall efficiency and functionality.
Improved Durability: Gears designed for specific operating conditions tend to last longer and perform better. Tailored solutions provide durability and reliability in demanding environments.
Case Studies Showcasing Successful Implementations
Numerous industries have benefited from customized gear solutions:
Automotive Industry: Custom gears in high-performance vehicles improve power transmission and fuel efficiency. These gears are designed for precision and reliability.
Manufacturing: Specialized gears in machinery enhance precision and reduce downtime, increasing productivity and operational efficiency.
Aerospace: Tailor-made gears withstand extreme conditions, ensuring reliability and safety in aircraft. Custom gears meet stringent aerospace standards for performance and durability.
Future Trends in Gear Technology
Emerging Trends and Future Innovations in Gear Manufacturing
The future of gear technology is promising, with emerging trends such as:
Smart Gears: Incorporating sensors to monitor performance and predict maintenance needs. Smart gears provide real-time data for proactive maintenance.
Advanced Materials: Continued development of stronger, lighter materials for better performance. Advanced materials offer improved efficiency and durability.
AI and Machine Learning: Using AI to design gears with optimized shapes and stress distribution. AI-driven designs enhance performance and reduce production costs.
The Role of Sustainable Practices in Gear Production
Sustainability is becoming increasingly important in gear production. Manufacturers are adopting eco-friendly practices, such as:
Recycling: Using recycled materials to produce gears, reducing environmental impact. Recycling promotes sustainability and resource conservation.
Energy Efficiency: Implementing energy-efficient manufacturing processes to lower carbon footprints.
Energy-efficient practices support environmental and economic goals.
Waste Reduction: Minimizing waste through precision manufacturing and additive techniques. Reducing waste helps protect the environment and improves manufacturing efficiency.
By embracing these sustainable practices, the gear industry can contribute to a greener future while maintaining high standards of performance and reliability. Investing in efficient and reliable gear solutions is crucial for maximizing the performance and longevity of industrial machinery, ensuring seamless operation and long-term success.
Investing in efficient and reliable gear solutions is vital for maximizing the performance and longevity of industrial machinery. By staying informed about the latest advancements and adopting best practices in gear maintenance, businesses can ensure the seamless operation of their mechanical systems and achieve long-term success.
Stay ahead of the curve by choosing cutting-edge gear solutions tailored to your specific needs. Contact us today to learn more about our range of high-quality, customized gear systems designed to enhance your machinery’s performance and reliability.