Gear Roll Testing: Enhancing Precision in Gear Manufacturing
How Gear Roll Testing Enhances Precision in Gear Manufacturing The Importance of Gear Roll Testing in Precision Manufacturing In the competitive landscape of gear manufacturing, precision is critical. Gears are foundational to countless mechanical systems, and even slight inaccuracies can disrupt performance. This is where gear roll testing proves indispensable. By assessing parameters such as […]

How Gear Roll Testing Enhances Precision in Gear Manufacturing
The Importance of Gear Roll Testing in Precision Manufacturing
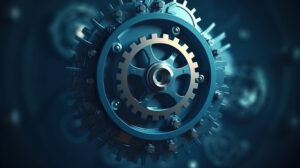
In the competitive landscape of gear manufacturing, precision is critical. Gears are foundational to countless mechanical systems, and even slight inaccuracies can disrupt performance. This is where gear roll testing proves indispensable.
By assessing parameters such as gear tooth alignment, noise levels, and dimensional accuracy, gear roll testing ensures that gears meet stringent quality standards. This process is vital for industries like automotive, aerospace, and industrial automation, where precision dictates performance and safety.
Let’s delve deeper into how gear roll testing enhances precision in manufacturing.
What is Gear Roll Testing?
Understanding the Gear Roll Testing Process
Gear roll testing is a specialized quality assurance process. It involves rolling a manufactured gear against a highly precise master gear to detect defects in parameters like pitch, tooth alignment, and gear noise.
Steps in the gear roll testing process:
- Alignment Check: Verifies proper engagement of gear teeth.
- Parameter Measurement: Tests factors such as helix angle and tooth thickness using advanced instruments.
- Load Simulation: Evaluates gear performance under stress conditions.
Gear roll testing helps manufacturers ensure that their products meet operational standards, eliminating inaccuracies before final production.
Why Gear Roll Testing is Essential
The Critical Role of Precision in Gear Roll Testing
In manufacturing, even a minor deviation in gear geometry can lead to:
- Increased vibrations
- Noise generation
- Accelerated wear and tear
Gear roll testing minimizes these risks by:
- Detecting errors in pitch or profile geometry
- Verifying proper tooth engagement
- Ensuring smoother operation and prolonged gear life
For industries like automotive and aerospace, where precision drives innovation, gear roll testing serves as a cornerstone of quality control.
Key Components of Gear Roll Testing
Components that Enhance Gear Roll Testing Precision
Gear roll testing relies on precise tools and components to deliver accurate results:
- Master Gears: Calibrated to the highest precision, these are the gold standard in the process.
- Measurement Tools: Instruments like micrometers and calipers detect minor deviations.
- Testing Machines: Assess critical parameters, including gear noise and alignment.
- Load Testing Equipment: Simulates real-world stresses, ensuring gears meet performance expectations.
These tools and components collectively enhance the reliability of gear roll testing.
Best Practices in Gear Roll Testing
Tips to Ensure Testing Accuracy
Adopting industry best practices ensures high precision in gear roll testing:
- Regular Calibration: Keeps all testing tools accurate.
- Master Gear Quality: High-precision master gears improve testing outcomes.
- Controlled Environment: Consistent temperatures reduce testing anomalies.
- Operator Training: Skilled operators prevent errors.
- Data Documentation: Tracks quality trends for continuous improvement.
How Gear Roll Testing Extends Gear Longevity
The Long-Term Benefits of Accurate Testing
Precision testing minimizes wear and tear, resulting in longer-lasting gears. It also reduces machine downtime and maintenance costs. Gears tested for accuracy are better suited for demanding applications, ensuring reliability over time.
Gear Roll Testing: A Cornerstone of Precision Manufacturing
In gear production, precision is non-negotiable. Gear roll testing safeguards against misalignments, reduces noise, and improves overall performance. It is indispensable for industries demanding high reliability, ensuring that precision manufacturing meets the challenges of modern engineering.