Ensuring Quality and Precision in Gear Manufacturing
A Comprehensive Guide to ISO Gear Standards and Their Impact on Gear Technology In the world of gear technology, maintaining high standards of quality and precision is crucial. ISO gear standards play a vital role in this aspect, ensuring that gears manufactured globally adhere to consistent levels of performance and reliability. These standards cover […]
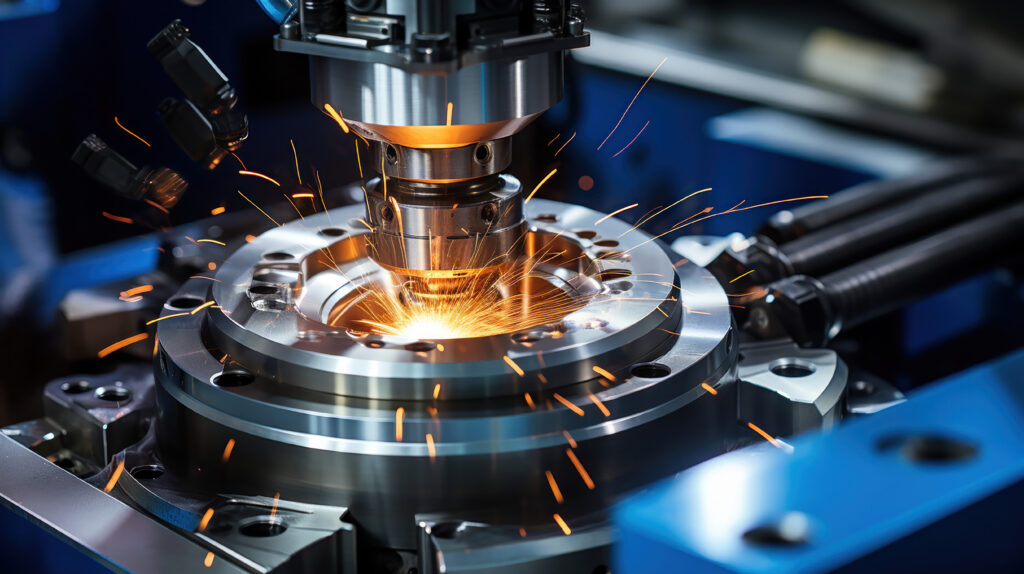
A Comprehensive Guide to ISO Gear Standards and Their Impact on Gear Technology
In the world of gear technology, maintaining high standards of quality and precision is crucial. ISO gear standards play a vital role in this aspect, ensuring that gears manufactured globally adhere to consistent levels of performance and reliability.
These standards cover various aspects of gear design, production, and testing, helping manufacturers produce gears that meet specific requirements and function efficiently in different applications. This article delves into the significance of ISO gear standards, their types, and their impact on the gear manufacturing industry.
What are ISO Gear Standards?
ISO (International Organization for Standardization) gear standards are internationally recognized guidelines that define the specifications, dimensions, and performance criteria for gears. These standards are developed through a consensus process involving experts from different countries, ensuring that they reflect the latest advancements and best practices in gear technology.
By adhering to ISO gear standards, manufacturers can ensure that their products are compatible with those produced by other manufacturers, facilitating global trade and collaboration.
Key ISO Gear Standards are specifically dedicated to gears. Some of the most important ones include:
ISO 1328-1:2013 – Cylindrical Gears: This standard specifies the tolerances for cylindrical gears gears, including spur and helical gears, focusing on the accuracy of the tooth profile, helix, pitch, and runout.
ISO 6336 – Calculation of Load Capacity of Spur and Helical Gears: This series of standards provides methods for calculating the load capacity of spur and helical gears, addressing factors such as tooth strength, surface durability, and scuffing.
ISO 14635 – FZG Test Procedures: These standards describe test methods for determining the scuffing load capacity of gear oils using the FZG (Forschungsstelle für Zahnräder and Getriebebau) test rig.
ISO 21771:2007 – Gears – Cylindrical Involute Gears and Gear Pairs: This standard specifies the geometry and dimensions of cylindrical involute gears and gear pairs, ensuring compatibility and interchangeability between gears from different manufacturers.
Importance of ISO Gear Standards: Ensuring Consistency and Quality
One of the primary benefits of ISO gear standards is the consistency they bring to gear manufacturing. By following these standards, manufacturers can produce gears with uniform dimensions and tolerances, reducing variability and ensuring high-quality products.
This consistency is essential for gears that need to work together in complex systems, such as automotive transmissions and industrial machinery.
Facilitating Global Trade
ISO gear standards also play a crucial role in facilitating global trade. When manufacturers adhere to these standards, their products become compatible with those made by other companies worldwide. This compatibility simplifies the process of sourcing gears and components from different suppliers, promoting international collaboration and reducing barriers to trade.
Enhancing Performance and Reliability
Gears manufactured according to ISO standards are designed to meet specific performance criteria, ensuring that they can withstand the stresses and loads they will encounter in their intended applications.
This focus on performance and reliability helps extend the lifespan of gears, reducing maintenance costs and downtime for end-users.
Implementing ISO Gear Standards: Design and Engineering
The implementation of ISO gear standards begins in the design and engineering phase. Gear designers must consider the specifications outlined in the relevant standards, ensuring that their designs meet the required tolerances and performance criteria.
This process often involves using advanced software tools for gear design and analysis, which can help optimize the geometry and dimensions of the gears.
Manufacturing Processes
Once the design is finalized, manufacturers must adhere to the prescribed standards during the production process. This adherence involves using precise machining techniques, such as hobbing, grinding, and shaping, to produce gears with the required accuracy. Quality control measures, including regular inspections and testing, are also crucial to ensure that the gears meet the ISO standards.
Testing and Validation
After manufacturing, gears must undergo rigorous testing to validate their performance and compliance with ISO standards. This testing can include dimensional inspections, load capacity tests, and surface durability assessments.
By thoroughly testing the gears, manufacturers can identify and address any issues before the products reach the market.
Challenges in Adopting ISO Gear Standards: Technological Advancements
One of the challenges in adopting ISO gear standards is keeping up with rapid technological advancements in gear technology. As new materials, manufacturing techniques, and design methods emerge, ISO standards must be regularly updated to reflect these changes. Staying abreast of these updates requires continuous learning and adaptation from gear manufacturers.
Compliance Costs
Implementing ISO gear standards can also involve significant costs, especially for small and medium-sized enterprises (SMEs). These costs include investments in advanced machinery, quality control equipment, and training for personnel.
However, the long-term benefits of improved product quality and marketability often outweigh the initial expenses. ISO gear standards are essential for ensuring the quality, consistency, and performance of gears used in various applications. By adhering to these standards, manufacturers can produce reliable and compatible gears that meet the demands of global markets.
Despite the challenges associated with adopting these standards, the benefits of enhanced product quality, facilitated trade, and improved performance make them invaluable to the gear manufacturing industry.
As technology continues to evolve, ongoing updates to ISO gear standards will be crucial to maintaining their relevance and effectiveness in promoting excellence in gear technology.