Comprehensive Guide to Thermal Processing in Gear Technology
Understanding the Importance of Thermal Processing in Gear Manufacturing Thermal processing in gear technology is crucial for enhancing the durability, wear resistance, and overall performance of gears. This comprehensive guide explores the various heat treatment methods used in gear manufacturing, ensuring your gears can withstand high stresses and perform efficiently in demanding applications. Let’s delve […]
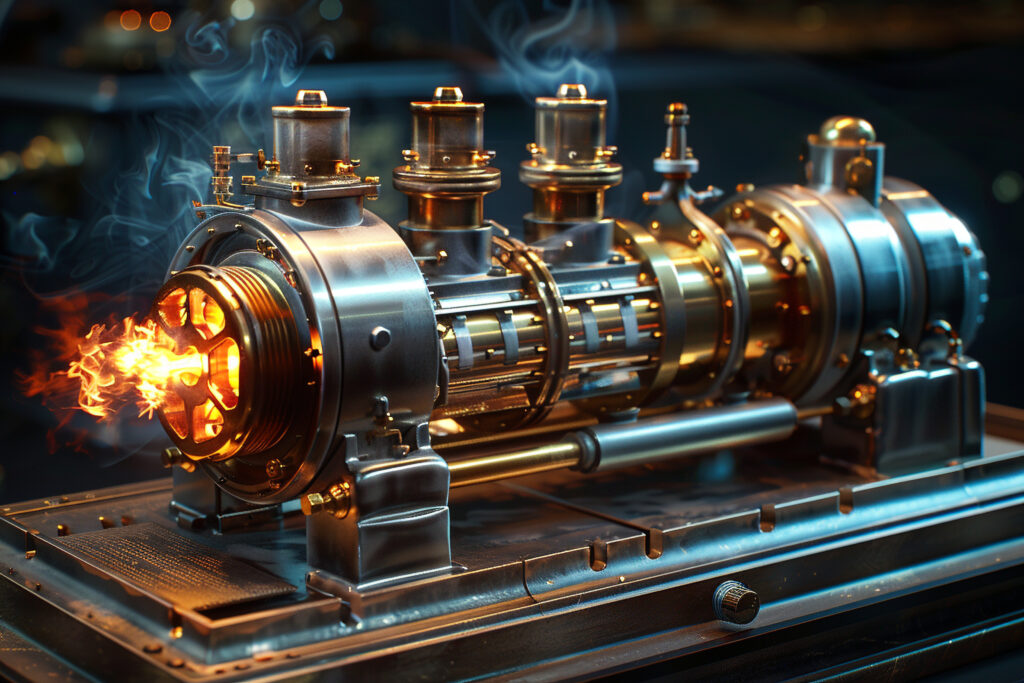
Understanding the Importance of Thermal Processing in Gear Manufacturing
Thermal processing in gear technology is crucial for enhancing the durability, wear resistance, and overall performance of gears. This comprehensive guide explores the various heat treatment methods used in gear manufacturing, ensuring your gears can withstand high stresses and perform efficiently in demanding applications.
Let’s delve into the key thermal processing techniques that play a vital role in gear technology.
Case Hardening: Strengthening Gear Surfaces for Longevity
Case hardening is a vital thermal processing technique that hardens the outer surface of the gear while keeping the inner core relatively softer and tougher. This method significantly improves the gear’s wear resistance and fatigue strength, making it ideal for high-stress applications.
Carburizing: Infusing Carbon for a Harder Surface
Carburizing involves heating the gear in a carbon-rich environment, allowing carbon atoms to diffuse into the surface. This process is followed by quenching to harden the surface. Carburizing creates a hard, wear-resistant outer layer while maintaining a tough core, ensuring the gear can handle heavy loads and repeated stress.
Nitriding: Enhancing Surface Hardness with Nitrogen
Nitriding introduces nitrogen into the surface of the gear at high temperatures, forming a hard nitride layer. This method enhances surface hardness without the need for quenching, reducing the risk of distortion. Nitrided gears are known for their excellent wear resistance and fatigue strength, making them suitable for high-performance applications.
Carbonitriding: Combining Carbon and Nitrogen for Superior Strength
Carbonitriding is a combination of carburizing and nitriding, where both carbon and nitrogen are diffused into the surface. This dual infusion results in a hardened surface with superior wear resistance and fatigue strength. Carbonitrided gears are highly durable, making them ideal for applications requiring high surface hardness and core toughness.
Through Hardening: Achieving Uniform Hardness in Gears
Through hardening, unlike case hardening, involves hardening the entire gear, not just the surface. This process entails heating the gear to a high temperature and then rapidly cooling (quenching) it. Through-hardened gears exhibit uniform hardness and strength throughout their structure, making them highly resistant to wear and deformation.
However, through-hardened gears may be more brittle compared to case-hardened gears. Therefore, they are typically used in applications where high strength and hardness are paramount, but the risk of impact or shock loads is minimal.
Induction Hardening: Precise Surface Hardening for Targeted Areas
Induction hardening is a localized heat treatment process where an electromagnetic field rapidly heats the gear’s surface. After heating, the gear is quenched to form a hardened layer. This method allows for precise control over the hardening depth and location, making it ideal for gears with complex geometries or specific areas requiring enhanced hardness.
Induction-hardened gears exhibit excellent wear resistance and fatigue strength, particularly in critical areas subject to high stress. This method is widely used in automotive and industrial applications where precise hardening is essential.
Tempering: Reducing Brittleness While Retaining Hardness
After hardening, gears often exhibit excessive brittleness, which can compromise their performance. Tempering is a heat treatment process that involves reheating the gear to a lower temperature and then cooling it slowly.
This process reduces brittleness while retaining much of the hardness and strength achieved through hardening. Tempered gears offer a balanced combination of hardness and toughness, making them suitable for applications requiring both wear resistance and impact strength.
Tempering is a crucial step in ensuring gears can withstand real-world operational stresses without failure.
Annealing: Enhancing Machinability and Reducing Internal Stresses
Annealing involves heating the gear to a high temperature and then cooling it slowly. This process relieves internal stresses, improves machinability, and refines the grain structure of the gear material. Annealed gears are easier to machine and form, making them ideal for subsequent manufacturing processes.
By reducing internal stresses, annealing also enhances the dimensional stability and overall quality of the gear. This method is often used in the initial stages of gear manufacturing to prepare the material for further heat treatment and machining.
Normalizing: Refining Grain Structure for Improved Properties
Normalizing involves heating the gear to a specific temperature and then air cooling it. This process refines the grain structure, enhances mechanical properties, and prepares the gear for further heat treatment. Normalized
gears exhibit improved toughness and uniformity, making them suitable for demanding applications.
The normalization process helps achieve a uniform microstructure, reducing the risk of defects and in consistencies in the final product. It is a critical step in producing high-quality gears with reliable performance characteristics.
Cryogenic Treatment: Boosting Hardness and Wear Resistance
Cryogenic treatment involves cooling the gear to extremely low temperatures (below -100°C) to transform retained austenite into marten site. This transformation improves the hardness and wear resistance of the gear, making it more durable and long-lasting.
Cryogenically treated gears exhibit enhanced performance in applications where high wear resistance and dimensional stability are essential. This advanced thermal processing method is often used in high-precision and high-performance gear manufacturing.
Optimizing Gear Performance with Thermal Processing
Thermal processing in gear technology is essential for producing gears that meet the demanding requirements of modern applications. By employing various heat treatment methods such as case hardening, through hardening, induction hardening, tempering, annealing, normalizing, and cryogenic treatment, manufacturers can enhance the properties of gears, ensuring they are durable, wear-resistant, and capable of withstanding high stresses.
Understanding and implementing the appropriate thermal processing techniques are crucial for optimizing gear performance and longevity. Whether for automotive, aerospace, or industrial machinery applications, thermal processing plays a pivotal role in ensuring gears operate efficiently and reliably under challenging conditions.
By leveraging these advanced heat treatment methods, manufacturers can produce high-quality gears that contribute to the overall success and reliability of their machinery and equipment. Thermal processing remains a cornerstone of gear technology, driving innovation and excellence in gear manufacturing.