Advancements in Gear Technology: Revolutionizing Mechanical Systems
Revolutionizing Gear Technology: Innovations in Materials and Manufacturing In the dynamic world of mechanical engineering, gear technology has undergone significant advancements. These innovations have transformed various industries, from automotive to aerospace, enhancing performance, efficiency, and durability. The latest developments in gear technology, exploring how these advancements are revolutionizing mechanical systems. Gears are fundamental components in […]
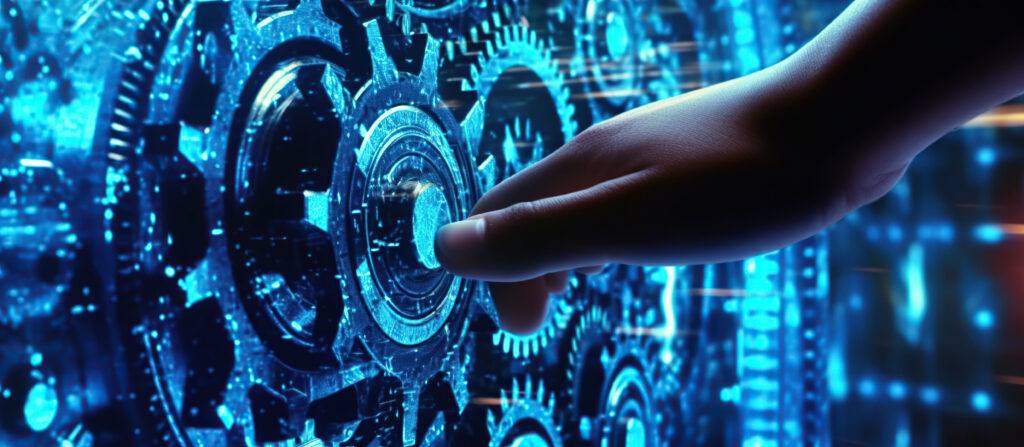
Revolutionizing Gear Technology: Innovations in Materials and Manufacturing
In the dynamic world of mechanical engineering, gear technology has undergone significant advancements. These innovations have transformed various industries, from automotive to aerospace, enhancing performance, efficiency, and durability.
The latest developments in gear technology, exploring how these advancements are revolutionizing mechanical systems. Gears are fundamental components in mechanical systems, facilitating the transfer of torque and motion between machine parts.
They play a crucial role in a wide range of applications, from simple mechanisms like clocks to complex systems in automobiles and aircraft. As technology progresses, the demand for more efficient and reliable gears increases, driving innovation in gear design, materials, and manufacturing processes.
High-Performance Gear Materials
One of the significant advancements in gear technology is the development of high-performance materials. Traditional gears were typically made from steel, which, although strong, had limitations in terms of weight and wear resistance. Modern gear materials include advanced composites, ceramics, and high-strength alloys that offer superior properties.
Composite Materials
Composite materials, such as carbon fiber-reinforced polymers, have become increasingly popular in gear manufacturing. These materials are lightweight yet incredibly strong, reducing the overall weight of gear systems while maintaining or even enhancing their strength.
This weight reduction is particularly beneficial in automotive and aerospace applications, where efficiency and fuel economy are paramount.
Ceramic Gears
Ceramic gears are another innovative development in gear technology. These gears are known for their exceptional hardness and resistance to wear and corrosion. Ceramics can operate at higher temperatures and with less lubrication compared to metal gears, making them ideal for high-stress environments. Additionally, ceramic gears exhibit lower friction, contributing to improved efficiency and longevity.
Precision Gear Manufacturing Techniques
Advancements in manufacturing techniques have also played a crucial role in the evolution of gear technology. Precision manufacturing processes ensure that gears meet stringent tolerances and performance standards, resulting in smoother and more reliable mechanical systems.
Additive Manufacturing
Additive manufacturing, commonly known as 3D printing, has revolutionized gear production. This technology allows for the creation of complex gear geometries that were previously impossible or too costly to produce using traditional methods. Additive manufacturing also enables rapid prototyping, reducing the time and cost associated with developing new gear designs.
Computer Numerical Control (CNC) Machining
CNC machining has become a cornerstone of modern gear manufacturing. This technology uses computer-controlled tools to precisely cut and shape gears, ensuring high levels of accuracy and consistency. CNC machining is particularly advantageous for producing gears with intricate designs and tight tolerances, essential for high-performance applications.
Advanced Gear Design and Analysis
The design and analysis of gears have been significantly enhanced by advancements in computer-aided engineering (CAE) software. These tools enable engineers to simulate and optimize gear performance, identifying potential issues and making necessary adjustments before physical production begins.
Finite Element Analysis (FEA)
Finite element analysis is a powerful tool used to predict how gears will perform under various conditions. By breaking down a gear into smaller elements, FEA allows engineers to analyze stress, strain, and deformation in great detail. This insight helps in designing gears that can withstand high loads and harsh operating environments.
Gear Dynamics Simulation
Gear dynamics simulation software models the behavior of gears in real-time, considering factors such as load distribution, vibration, and noise. These simulations are crucial for optimizing gear designs to ensure smooth operation and minimize wear and tear. As a result, gears can be designed to operate more quietly and with greater efficiency.
Surface Treatments and Coatings
Surface treatments and coatings are essential for enhancing the performance and longevity of gears. These processes improve the wear resistance, corrosion resistance, and friction properties of gear surfaces.
Hardening Processes
Surface hardening processes, such as carburizing and nitriding, increase the hardness of gear surfaces, making them more resistant to wear and fatigue. These treatments extend the lifespan of gears, particularly in high-load and high-speed applications.
Advanced Coatings
Advanced coatings, such as diamond-like carbon (DLC) and tungsten carbide, provide exceptional wear resistance and low friction. These coatings are applied using techniques like physical vapor deposition (PVD) and chemical vapor deposition (CVD), creating a durable surface layer that enhances gear performance.
Applications of Advanced Gear Technology

The advancements in gear technology have broad implications across various industries. Here are some notable applications:
Automotive Industry
In the automotive industry, advanced gear technology is crucial for improving fuel efficiency and performance. Lightweight composite gears reduce the weight of transmission systems, while precision manufacturing ensures smooth and reliable operation. Additionally, surface treatments and coatings enhance the durability of gears, reducing maintenance costs and increasing the lifespan of vehicles.
Aerospace Industry
The aerospace industry benefits greatly from advanced gear technology. High-performance materials, such as composites and ceramics, reduce the weight of aircraft, improving fuel efficiency and payload capacity.
Precision manufacturing and advanced design tools ensure that gears can withstand the extreme conditions of flight, including high loads and temperatures.
Robotics and Automation
In robotics and automation, advanced gears are essential for achieving precise and reliable motion control. Precision manufacturing techniques enable the production of gears with tight tolerances, ensuring smooth and accurate movements. Additionally, advanced coatings and surface treatments reduce friction and wear, extending the lifespan of robotic components.
The advancements in gear technology are revolutionizing mechanical systems, offering significant improvements in performance, efficiency, and durability.
High-performance materials, precision manufacturing techniques, advanced design tools, and innovative surface treatments are driving these developments, enabling gears to meet the increasing demands of modern applications.
As gear technology continues to evolve, we can expect even greater innovations that will further enhance the capabilities of mechanical systems across various industries.