Gear Grinding: Boosting Efficiency & Cutting Downtime
Enhance Gear Grinding Efficiency with Optimized Techniques Boost Gear Grinding Performance with Advanced Techniques Is your gear grinding process holding back your manufacturing output? Many manufacturers struggle with outdated grinding techniques that lead to high downtime and low productivity. Optimizing gear grinding can drastically improve operational efficiency, reduce costs, and extend equipment lifespan. Gear grinding […]
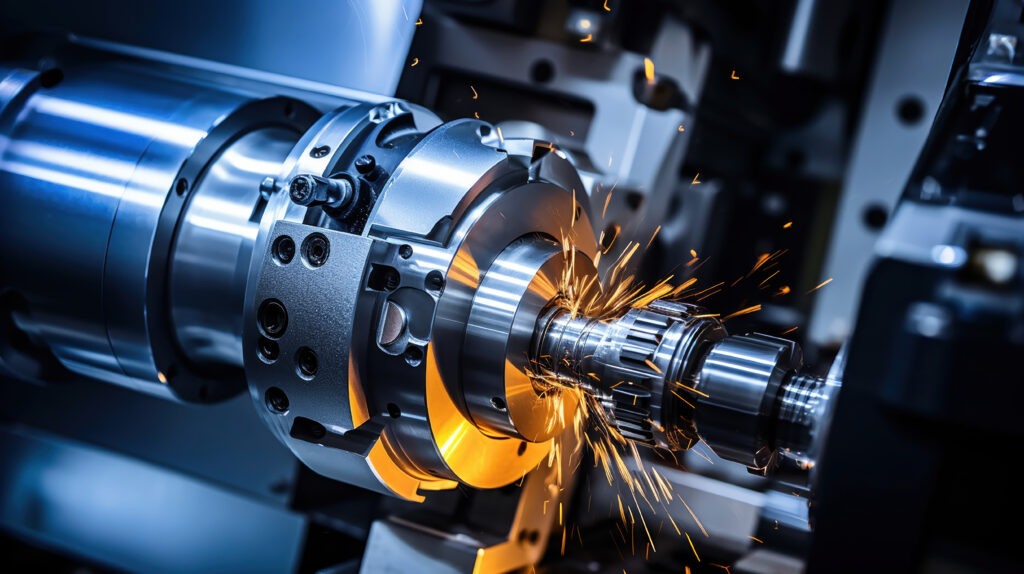
Enhance Gear Grinding Efficiency with Optimized Techniques
Boost Gear Grinding Performance with Advanced Techniques
Is your gear grinding process holding back your manufacturing output? Many manufacturers struggle with outdated grinding techniques that lead to high downtime and low productivity. Optimizing gear grinding can drastically improve operational efficiency, reduce costs, and extend equipment lifespan.
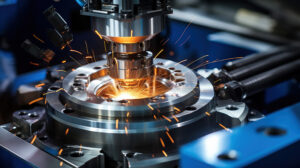
Gear grinding is a critical machining process used in the manufacturing and maintenance of precision gears across various industrial applications. When done correctly, it ensures that the gear teeth mesh efficiently, leading to smoother operation, reduced wear, and a longer gear lifespan.
However, many industries continue to face inefficiencies due to outdated gear grinding processes. These inefficiencies often result in lower productivity, increased maintenance costs, and reduced product quality.
In this comprehensive guide, we explore the latest advancements in gear grinding techniques. We will provide valuable insights into how you can revolutionize your production line by embracing optimized grinding processes that enhance performance and reduce downtime.
Understanding the Importance of Optimized Gear Grinding
Optimized gear grinding is essential for industries that rely on high-precision gears. The role of gears in any mechanical system cannot be overstated, as they are fundamental components that determine the overall efficiency, noise, vibration, and performance of machinery.
There are several key benefits of optimizing your gear grinding process:
- Enhanced Gear Accuracy: Precision gear grinding ensures that the gear teeth are perfectly shaped to mesh smoothly. This reduces friction, wear, and energy loss during operation.
- Improved Surface Finish: A well-ground gear has a smoother surface, which reduces friction, noise, and heat during operation. This improves the lifespan of the gear and the machinery it operates within.
- Correcting Manufacturing Errors: Gear grinding can correct small imperfections from the initial manufacturing process, ensuring that gears meet tight specifications for high-performance machinery.
- Extending Gear Life: By optimizing tooth profiles and surface quality, optimized gear grinding significantly increases the operational lifespan of gears.
- Maintaining Gear Performance: Gears that undergo regular grinding services continue to perform at optimal levels throughout their lifecycle, preventing issues related to misalignment or poor engagement.
By ensuring high levels of accuracy, surface finish, and longevity, optimized gear grinding supports not only individual gear performance but also the overall efficiency of mechanical systems.
Key Components of Gear Grinding: Essential Elements for Successful Gear Grinding
Gear grinding is a sophisticated process that requires precision equipment and tools. Several key components work together to ensure that gears are ground to the desired level of accuracy and quality. These components include:
- Grinding Wheels:
Grinding wheels are made from abrasive materials like aluminum oxide, cubic boron nitride (CBN), and diamond. The selection of material, hardness, grain size, and bonding type plays a crucial role in determining the effectiveness of the grinding process. For instance, CBN is preferred for hardened steels due to its excellent hardness and heat resistance, while aluminum oxide is used for general-purpose grinding. - Work holding Devices:
These devices secure the gear during the grinding process to ensure accuracy and stability. Common types of workholding devices include centers, chucks, and specialized fixtures designed to hold different types of gears securely. - Dressing Tools:
Dressing tools maintain the shape and sharpness of the grinding wheel. Proper dressing is crucial to ensuring that the grinding wheel performs effectively over time. Single-point diamond dressers, rotary dressers, and crush roll dressers are commonly used to dress grinding wheels. - Coolant System:
The role of the coolant system is to regulate temperature during the grinding process and remove debris from the grinding area. Proper coolant flow ensures that the grinding operation remains efficient, and it helps in maintaining the structural integrity of both the grinding wheel and the gear being machined. - Control Systems:
Modern gear grinding machines are equipped with CNC controls and process monitoring sensors that allow operators to control grinding parameters with high precision. These systems ensure that the grinding process is consistent and meets the required specifications. - Measurement and Inspection Equipment:
The quality of ground gears must be verified using advanced inspection tools such as coordinate measuring machines (CMMs), gear analyzers, and profile projectors. These tools help ensure that the finished gears meet the required dimensional tolerances and surface finish specifications.
Grinding Wheel Material Comparison Table: Grinding Wheel Material Properties for Gear Grinding
Material |
Hardness | Heat Resistance | Typical Applications | Cost |
Aluminum Oxide |
Moderate | Good | General-purpose grinding | Low |
Silicon Carbide |
High | Excellent | High-speed grinding of hardened materials | Moderate |
Cubic Boron Nitride (CBN) |
Very High | Excellent | Precision grinding of hardened steels | High |
Diamond |
Extremely High | Poor | Grinding of carbide and ceramic materials | Very High |
Selecting the right grinding wheel material is critical for achieving the desired level of precision and efficiency in gear grinding. Each material offers distinct advantages, depending on the specific application and material of the gear being ground.
Impact on Industrial Efficiency : How Gear Grinding Enhances Industrial Productivity
Gear grinding plays a pivotal role in enhancing the overall productivity and efficiency of industrial operations. By improving the performance and reliability of gears, manufacturers can achieve significant cost savings and operational benefits.
- Increased Equipment Uptime:
Gears that are ground to high precision experience less wear and tear, resulting in fewer unplanned breakdowns and increased machine uptime. This allows manufacturers to maintain consistent production levels and meet tight deadlines. - Energy Efficiency:
Precision-ground gears operate with reduced friction, leading to lower energy consumption. This is particularly important in large-scale industrial operations where even minor improvements in energy efficiency can lead to substantial cost savings. - Extended Equipment Lifespan:
Regular service gear grinding can significantly extend the operational life of gear-driven machinery. By reducing wear on gears, manufacturers can delay the need for costly replacements or major overhauls, leading to long-term cost savings. - Improved Product Quality:
In industries such as automotive, aerospace, and manufacturing automation, the quality of gears directly affects the performance of the end product. Optimized gear grinding results in higher precision and better-quality products, leading to greater customer satisfaction and reduced warranty claims. - Noise Reduction:
Precision-ground gears generate less noise during operation, creating a quieter working environment. This can improve the overall work conditions for employees and reduce the need for expensive noise mitigation measures.
Case Studies : Real-World Examples of Gear Grinding Efficiency
- Automotive Manufacturing:
In automotive manufacturing, the performance of gears in transmissions is critical for fuel efficiency and smooth operation. Precision-ground gears improve transmission performance, reduce noise, and contribute to better vehicle quality. - Wind Energy Production:
In wind energy, the efficiency of gearboxes directly affects the energy output of wind turbines. By using precision-ground gears, wind farms can increase energy conversion efficiency, reduce maintenance costs, and minimize downtime. - Aerospace:
The aerospace industry relies on ultra-precise gears for aircraft engines and control systems. Precision-ground gears ensure safety, reliability, and improved fuel efficiency, making them essential components in modern aircraft.
Advanced Techniques in Gear Grinding : Innovative Methods to Improve Gear Grinding
- Continuous Dress Creep Feed (CDCF) Grinding:
CDCF is an advanced gear grinding technique that combines the benefits of creep feed grinding with continuous dressing. This method allows for greater precision and faster cycle times. It is particularly effective for grinding hardened gears, where maintaining tooth profiles and surface finishes is crucial. - High-Speed Grinding:
High-speed grinding involves increasing the cutting speed of the grinding wheel. This technique improves surface finish, reduces cycle times, and lowers grinding forces, making it a preferred method for high-volume production environments. - Dry Grinding Methods:
Dry grinding, which eliminates the use of coolant, offers environmental benefits and cost savings. Although dry grinding generates more heat, advancements in grinding wheel materials and air-based chip evacuation systems have made it a viable option for certain applications. - Intelligent Process Monitoring Systems:
These systems use real-time data from sensors to optimize the grinding process. Intelligent monitoring helps reduce scrap rates, improve quality, and prevent machine breakdowns. By using advanced analytics and machine learning, these systems can adjust grinding parameters on the fly to ensure optimal results.
Maximizing Gear Grinding Efficiency for Long-Term Success
Optimizing your gear grinding process is essential for enhancing efficiency, reducing downtime, and improving the overall quality of your production line. By implementing advanced techniques and using appropriate grinding tools, manufacturers can achieve significant cost savings and improved performance.
Incorporating these strategies ensures that your manufacturing processes stay competitive and productive in today’s fast-paced industrial environment.