Rise of Advanced Composites in Gear Manufacturing
The gear manufacturing industry is undergoing a significant transformation with the increasing adoption of advanced composite materials. These materials offer superior strength, lightweight properties, and enhanced durability compared to traditional metals, driving their popularity in various applications, including automotive, aerospace, and industrial machinery. The benefits of advanced composites in gear manufacturing, the latest technological […]
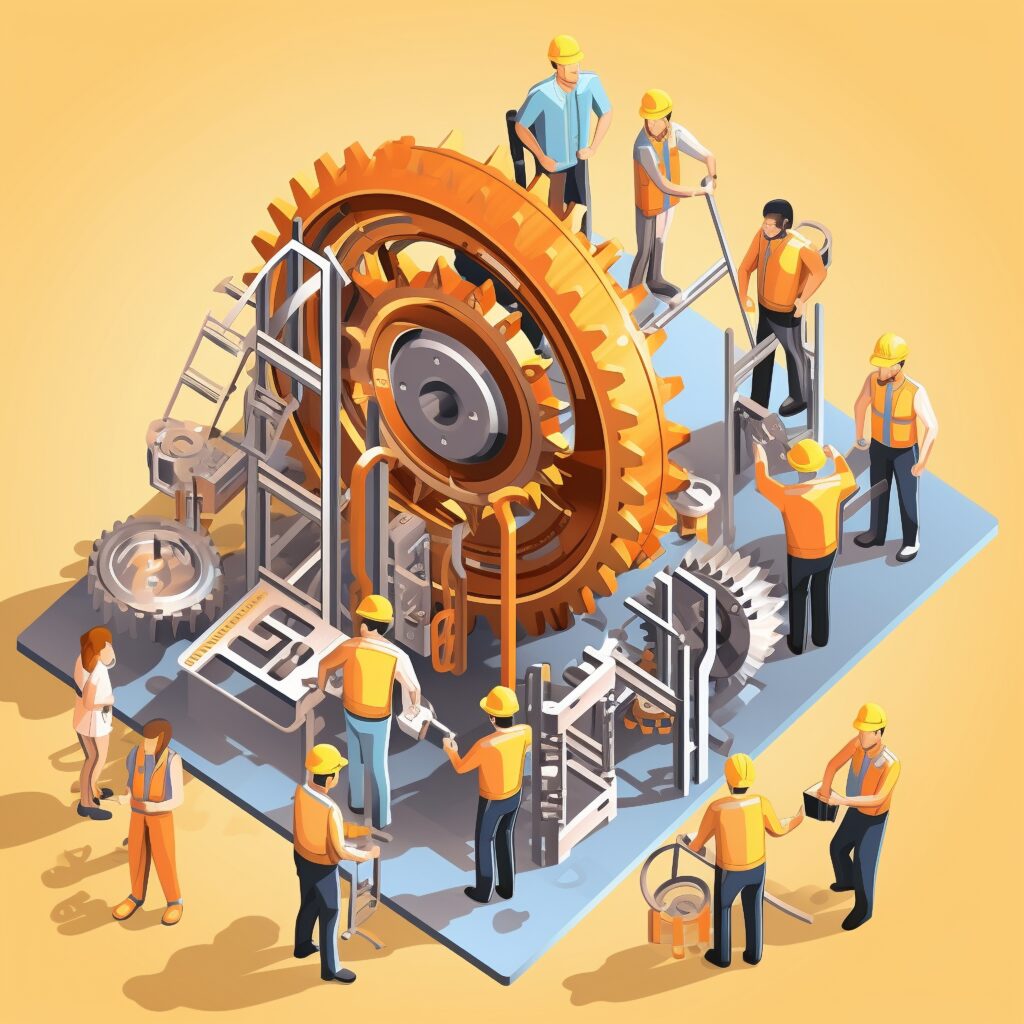
The gear manufacturing industry is undergoing a significant transformation with the increasing adoption of advanced composite materials.
These materials offer superior strength, lightweight properties, and enhanced durability compared to traditional metals, driving their popularity in various applications, including automotive, aerospace, and industrial machinery.
The benefits of advanced composites in gear manufacturing, the latest technological advancements, and their impact on production efficiency and performance.
By embracing these innovative materials, manufacturers can achieve higher precision, reduce wear and tear, and enhance the overall lifespan of gears, leading to cost savings and improved reliability.
Benefits of Composite Materials for Gears
Advanced composites in gear manufacturing have revolutionized the industry by providing numerous benefits. One of the most significant advantages of composite materials for gears is their lightweight nature.
Traditional metal gears are often heavy, which can reduce the efficiency of the machinery they are part of. In contrast, lightweight gear materials, such as composites, reduce the overall weight of the system, leading to improved efficiency and lower energy consumption.
Another key benefit is the superior strength and high-strength composite gears. These materials are designed to with stand higher stress and strain levels than their metal counterparts, making them ideal for applications requiring high durability. This increased durability of composite gears results in less frequent replacements and maintenance, further contributing to cost savings in gear manufacturing.
Latest Technological Advancements in Gear Manufacturing
The field of gear manufacturing technology has seen significant innovations in recent years, primarily driven by the development and application of advanced composites. Innovations in gear manufacturing include the use of cutting-edge materials and techniques to enhance the performance and lifespan of gears. For example, the integration of carbon fiber composites in gear production has led to gears that are not only lighter but also more robust and resistant to wear.
Additionally, advancements in manufacturing processes, such as 3D printing and automated fiber placement, have allowed for more precise and efficient production of composite gears. These technologies enable manufacturers to create complex geometries and designs that were previously unattainable with traditional manufacturing methods.
This precision in gear production efficiency ensures that the gears perform optimally in their respective applications.
Applications of Composite Gears in Various Industries
The versatility of composite materials for gears has led to their adoption across various industries. In the automotive sector, automotive gear composites are increasingly used to produce lighter and more fuel-efficient vehicles. Composite gears contribute to reducing the overall weight of the vehicle, thereby improving its fuel economy and reducing emissions.
In the aerospace industry, aerospace composite gears are essential for creating lighter and more durable aircraft components. The high strength-to-weight ratio of composite materials makes them ideal for aerospace applications, where weight reduction is crucial for improving flight performance and fuel efficiency.
Industrial machinery gears made from composites are also gaining traction due to their ability to withstand harsh operating conditions. These gears are used in various types of machinery, including heavy-duty industrial equipment, where they offer improved performance and longevity compared to traditional metal gears.
Enhancing Gear Lifespan and Performance
One of the primary goals of using advanced composites in gear manufacturing is to improve the lifespan and performance of gears. Composite gear advantages include their resistance to corrosion and wear, which are common issues with metal gears. This resistance to environmental factors ensures that composite gears maintain their performance over a more extended period.
Furthermore, the ability to tailor the properties of composite materials allows manufacturers to optimize gears for specific applications. By selecting the appropriate combination of fibers and resins, it is possible to create gears with enhanced mechanical properties, such as increased toughness and reduced friction. This customization leads to gear lifespan improvement and better overall performance.
Economic Impact of Advanced Composite Gears
The adoption of advanced composites in gear manufacturing has a significant economic impact on the industry. While the initial cost of composite materials may be higher than traditional metals, the long-term benefits far outweigh the initial investment. The durability and reduced maintenance requirements of composite gears lead to cost savings in gear manufacturing over time.
Additionally, the improved efficiency and performance of machinery equipped with composite gears contribute to lower operational costs. The reduced energy consumption and increased productivity of these machines result in a more competitive and profitable manufacturing process.
This economic advantage makes the adoption of composite gears an attractive option for manufacturers looking to optimize their operations.
Future Trends and Developments in Composite Gear Manufacturing
As the technology and materials used in gear manufacturing continue to evolve, the future of composite gear manufacturing looks promising. Researchers and engineers are continuously exploring new materials and methods to further enhance the performance and efficiency of composite gears. For example, the development of nano-composites, which incorporate nanoparticles into the composite matrix, holds great potential for creating even stronger and more durable gears.
Another area of focus is the sustainability of composite materials. As industries strive to reduce their environmental footprint, the use of recyclable and eco-friendly composite materials is becoming increasingly important. The development of bio-based composites, made from renewable resources, is an exciting trend that could shape the future of gear manufacturing.
Embracing the Composite Revolution
The rise of advanced composites in gear manufacturing marks a significant shift in the industry. With their superior strength, lightweight properties, and enhanced durability, composite materials for gears offer numerous benefits over traditional metals. The latest technological advancements in gear manufacturing technology have further propelled the adoption of these materials, resulting in improved production efficiency and performance.
The applications of composite gears in various industries, including automotive, aerospace, and industrial machinery, highlight their versatility and effectiveness. By embracing these innovative materials, manufacturers can achieve higher precision, reduce wear and tear, and enhance the overall lifespan of gears. This leads to cost savings, improved reliability, and a more competitive manufacturing process.
As the industry continues to evolve, the future of composite gear manufacturing looks bright. With ongoing research and development, new materials and technologies will continue to emerge, further enhancing the performance and sustainability of composite gears. By staying at the forefront of these advancements, manufacturers can remain competitive and capitalize on the numerous benefits that advanced composites have to offer.
The adoption of advanced composites in gear manufacturing is not just a trend but a revolution that is here to stay. Embracing this revolution will undoubtedly lead to a more efficient, cost-effective, and sustainable future for the gear manufacturing industry.